Process for synthesizing natural gas by methanation of coal synthesis gas
A coal-to-synthesis gas and chemical synthesis technology, which is applied in the petroleum industry, gas fuel, fuel, etc., can solve the problems of increasing equipment investment and achieve the effects of saving heat energy, increasing the selectivity of main products, and increasing the conversion rate of raw material gas
- Summary
- Abstract
- Description
- Claims
- Application Information
AI Technical Summary
Problems solved by technology
Method used
Image
Examples
Embodiment 1
[0028] Coal is gasified to produce coal gas, which is then transformed into methanation raw material gas, which is composed of (V%): H 2 -65, CO-21, CO 2 -1,CH 4 -12. First, the domestic J101 type methanation catalyst dispersed in the inert liquid phase medium (the catalyst concentration in the liquid phase is 30 wt%) in the fresh catalyst storage tank 5 is pressed into the slurry bed methanation reactor 1 from the bottom through the circulation pump 7 , then the composition becomes H 2 -10mol% and N 2 -90mol% reducing gas is introduced from the bottom of slurry bed methanation reactor 1 through pipeline p1, and after the temperature is raised to 400°C at a heating rate of 1°C / min, the catalyst is reduced at normal pressure. The reducing gas is switched to methane raw material gas, and the pressure is raised to 3Mpa at the same time, the temperature is adjusted to the reaction temperature, and the methanation reaction is carried out in the slurry bed methanation reactor 1,...
Embodiment 2~11
[0030]On the basis of Example 1, Examples 2-11 are about the catalyst type, the concentration of the catalyst in the slurry bed methanation reactor, the type of inert liquid medium, the composition of the reducing gas, the space velocity of the reducing gas, the reduction temperature, and the feed gas The hydrogen-carbon ratio, space velocity, reaction temperature, and reaction pressure factors have been adjusted. The specific data and results are shown in Attached Table 1, and the composition of raw material gas and product gas is shown in Attached Table 2.
[0031]
[0032] Schedule 2
[0033]
PUM
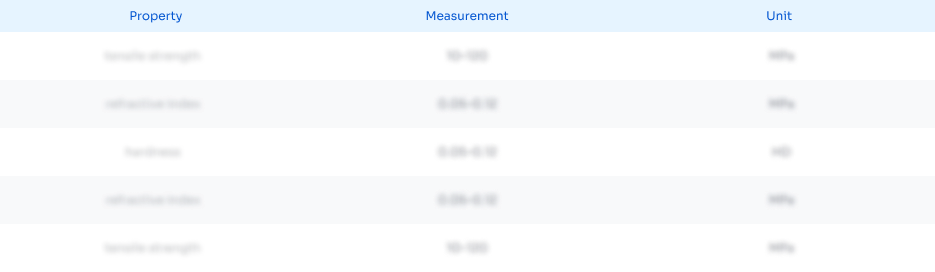
Abstract
Description
Claims
Application Information

- Generate Ideas
- Intellectual Property
- Life Sciences
- Materials
- Tech Scout
- Unparalleled Data Quality
- Higher Quality Content
- 60% Fewer Hallucinations
Browse by: Latest US Patents, China's latest patents, Technical Efficacy Thesaurus, Application Domain, Technology Topic, Popular Technical Reports.
© 2025 PatSnap. All rights reserved.Legal|Privacy policy|Modern Slavery Act Transparency Statement|Sitemap|About US| Contact US: help@patsnap.com