Separation method for producing light olefins from oxygenated chemicals
A separation method and technology of carbon olefins, applied in the direction of purification/separation of hydrocarbons, hydrocarbons, hydrocarbon cracking and hydrocarbon production, etc., can solve problems such as inappropriateness, achieve good applicability, reduce equipment investment and operation difficulty, and reduce equipment Effects of investment and energy consumption
- Summary
- Abstract
- Description
- Claims
- Application Information
AI Technical Summary
Problems solved by technology
Method used
Image
Examples
Embodiment 1
[0033] like figure 1, the low-carbon hydrocarbons from the reaction are cooled after heat recovery, compression and purification, and first enter the depropanizer under the conditions of 2.1MPa and 15°C. The demethanizer uses ethane as the absorbent, and the temperature of the ethane absorbent is -24°C. Table 1 is the calculation result of the problem. It can be seen from the table that when the mass flow rate of ethylene in the control light component is the same, the ethane absorbent required is less than the propane absorbent, and the ethane mass flow rate is only 2-3 of that of propane, although The loss of ethane with light components is much more than that of propane, but the lost ethane does not reduce its utilization value and can still be used as fuel gas. Using propane as absorbent, the loss of propane is 672kg-h, and the annual loss is 5376t. Originally propane can be sold as LPG by-product, but at this time it can only be used as fuel gas, which seriously reduces ...
Embodiment 2
[0035] like figure 2 , the low-carbon hydrocarbons from the reaction are cooled after heat recovery, compression and purification, and first enter the depropanizer under the conditions of 2.1MPa and 15°C, and the gas phase at the top of the depropanizer is compressed to 3.4MPa and cooled to -30°C. In the methane tower, due to the low selectivity of ethane in the product, if ethane is used as the absorbent, the amount of ethane lost with the light components is greater than that of the product ethane. If all ethane is used as the absorbent, part of the ethane needs to be purchased. Consider adding propane as absorbent at this time. It can also be seen from Table 2 that compared with the complete use of propane as absorbent, the total mass of absorbent is less, and the loss of propane is reduced by 560kg-h, and the annual loss of propane is reduced by about 4480t.
[0036] Table 1 embodiment 1 calculation result compares with completely using propane as absorbent
[0037] ...
PUM
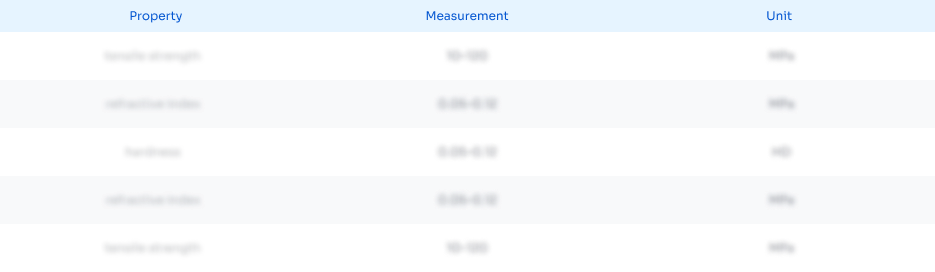
Abstract
Description
Claims
Application Information

- R&D
- Intellectual Property
- Life Sciences
- Materials
- Tech Scout
- Unparalleled Data Quality
- Higher Quality Content
- 60% Fewer Hallucinations
Browse by: Latest US Patents, China's latest patents, Technical Efficacy Thesaurus, Application Domain, Technology Topic, Popular Technical Reports.
© 2025 PatSnap. All rights reserved.Legal|Privacy policy|Modern Slavery Act Transparency Statement|Sitemap|About US| Contact US: help@patsnap.com