System-on-chip driver of high-subdivision multi-path stepping motor
A stepper motor, system-on-chip technology, applied in control systems, motor generator control, electrical components, etc., can solve the problems of low-frequency oscillation and high-frequency output, unable to meet the coordinated simultaneous operation of multiple stepper motors, etc., to reduce area, improve dynamic performance and motion position control accuracy, reduce system cost and power consumption
- Summary
- Abstract
- Description
- Claims
- Application Information
AI Technical Summary
Problems solved by technology
Method used
Image
Examples
specific Embodiment approach 1
[0049] Specific implementation mode one: the following combination Figure 1 to Figure 11 Describe this embodiment, this embodiment comprises dial switch 1, FPGA main control circuit 2, n road optocoupler isolation circuit 3, n road drive circuit 4, n road three-phase inverter bridge 5, 3n current transformers 6 and n-way overcurrent protection circuit 7,
[0050] The output terminal of the dial switch 1 is connected to the input terminal of the FPGA main control circuit 2, and the FPGA main control circuit 2 has n road motor output ports, and each road motor output port is connected to the input end of one road optocoupler isolation circuit 3, and the optocoupler isolation circuit 3 The output terminal of the circuit 3 is connected to the input terminal of the drive circuit 4, the output terminal of the drive circuit 4 is connected to the input terminal of the three-phase inverter bridge 5, and the three output terminals of the three-phase inverter bridge 5 are respectively t...
specific Embodiment approach 2
[0085] Specific implementation mode two: the following combination Figure 12 to Figure 31 Describe this implementation mode, this implementation mode gives specific examples, the experimental object of this system is a three-phase hybrid stepping motor, the model is: 57H370C2500. The base step angle is 1.2° / 0.6°, the phase current is 5.2A, the holding torque is 0.9N·m, and the no-load starting frequency is 2KHz.
[0086] The FPGA main control circuit 2 given in this embodiment provides n=8 motor control signals, but considering the system cost and practicability, only two-way stepper motor isolation drive hardware circuits are made, and only two-way motor drive performance is tested. Related tests, since the FPGA main control circuit 2 provides 8 control signals at the same time, all of them meet the control requirements after testing. Although only two stepper motors are controlled at the same time, it can represent the situation that 8 motors are driven at the same time.
...
PUM
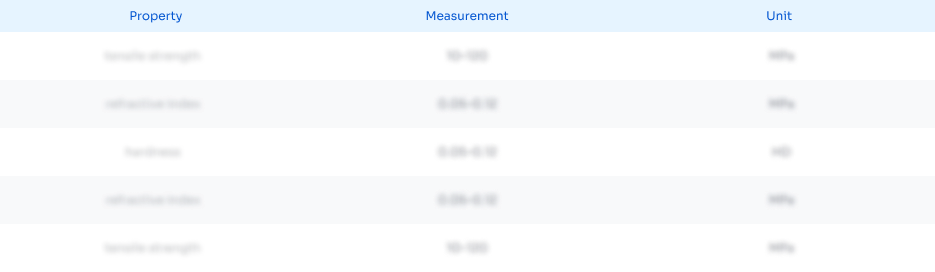
Abstract
Description
Claims
Application Information

- R&D
- Intellectual Property
- Life Sciences
- Materials
- Tech Scout
- Unparalleled Data Quality
- Higher Quality Content
- 60% Fewer Hallucinations
Browse by: Latest US Patents, China's latest patents, Technical Efficacy Thesaurus, Application Domain, Technology Topic, Popular Technical Reports.
© 2025 PatSnap. All rights reserved.Legal|Privacy policy|Modern Slavery Act Transparency Statement|Sitemap|About US| Contact US: help@patsnap.com