High-temperature oil heating system for vulcanizing machine
A heating system and high-temperature oil technology, applied in the field of vulcanizing machine heating system, can solve the problems of heat loss, harsh working environment, and large energy waste
- Summary
- Abstract
- Description
- Claims
- Application Information
AI Technical Summary
Problems solved by technology
Method used
Image
Examples
Embodiment Construction
[0021] Below in conjunction with accompanying drawing and embodiment the technical solution of the present invention is further described:
[0022] Such as figure 1 , figure 2 with image 3 The present invention as shown provides a high-temperature oil heating system for a vulcanizer, including: a mold table 1 provided with an oil chamber, heat transfer oil, a circulation pipeline 2, an electromagnetic induction heater 3, a high-temperature oil pump 4, an insulating oil tank 5, and a temperature Controller 6, temperature sensor 61, temperature display 62, heat insulation plate 12, insulation cover plate 13 and heat-resistant flange 21, heat insulation plate 12, insulation cover plate 13 are mainly made of glass fiber insulation cotton. Among them, the circulation pipeline 2 and the heat-resistant flange 21 are sequentially connected to the thermal oil tank 5, the high temperature oil pump 4, the electromagnetic induction heater 3 and the upper part of the mold table 1 accor...
PUM
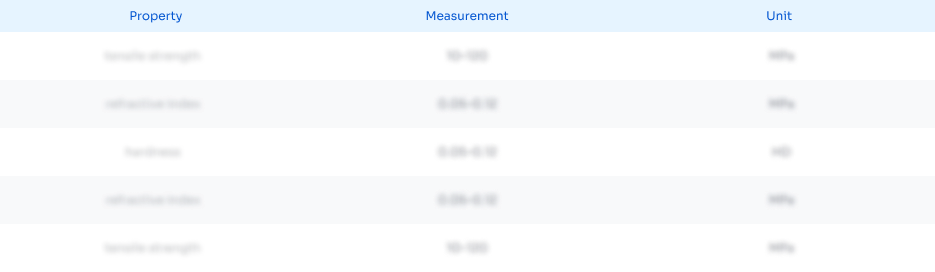
Abstract
Description
Claims
Application Information

- R&D
- Intellectual Property
- Life Sciences
- Materials
- Tech Scout
- Unparalleled Data Quality
- Higher Quality Content
- 60% Fewer Hallucinations
Browse by: Latest US Patents, China's latest patents, Technical Efficacy Thesaurus, Application Domain, Technology Topic, Popular Technical Reports.
© 2025 PatSnap. All rights reserved.Legal|Privacy policy|Modern Slavery Act Transparency Statement|Sitemap|About US| Contact US: help@patsnap.com