Method for preparing chloro-epoxy fatty acid methyl ester plasticizer
A technology of chlorinated epoxy fatty acid methyl ester and substituted epoxy fatty acid methyl ester, which is applied in the field of preparation of plasticizers for organic chemical products, and can solve problems such as poor compatibility, high production cost, and limited addition amount
- Summary
- Abstract
- Description
- Claims
- Application Information
AI Technical Summary
Problems solved by technology
Method used
Image
Examples
Embodiment 1
[0027] Embodiment 1: According to the weight ratio of raw materials, in a 1000-liter glass-lined stirred reactor, add 500 kg of biodiesel with an iodine value of 86.5 and 50 kg of acetic acid respectively, heat up to 45° C. under stirring, and stop heating for use.
[0028] Add 200 kg of hydrogen peroxide liquid with a mass percentage of 36% into the hydrogen peroxide metering and dropping tank, and slowly add the hydrogen peroxide liquid into a 1000-liter glass-lined stirring reactor under stirring conditions, and control the reaction temperature to 55 ° C, 2.5 After the hydrogen peroxide has been added within 1 hour, the material in the stirring reactor is then insulated and stirred for 2 hours, so that the epoxidation reaction in the kettle is fully and thoroughly obtained, and the epoxy intermediate product crude product (epoxy fatty acid methyl ester crude product) is obtained. Obtain epoxy intermediate product (epoxy fatty acid methyl ester) 505kg after separation, washin...
Embodiment 2
[0030] Embodiment 2: produce 25% acetic acid aqueous solution 70kg in embodiment 1 and mix with raw material acetic acid 35kg, and add in the glass-lined stirred reactor of 1000L together with the 500kg biodiesel of iodine number 85, other operation steps and technical control parameter are the same Embodiment 1, obtains epoxy intermediate product (epoxy fatty acid methyl ester) 502kg. Obtain final product (chlorinated epoxy type plasticizer) 603kg, and its chlorine content is 21.3%
Embodiment 3
[0031] Example 3: In a 1000-liter glass-lined stirred reactor, 500 kg of biodiesel with an iodine value of 82 and 50 kg of formic acid were respectively added, the temperature was raised to 42° C. under stirring, and the heating was stopped for use.
[0032] Add 150 kg of hydrogen peroxide liquid with a mass percentage of 50% to the hydrogen peroxide metering and dropping tank, and add the hydrogen peroxide to a 1000-liter glass-lined stirring reactor at a uniform speed under stirring conditions, and control the reaction temperature to 60 ° C for 2.0 hours After the addition of hydrogen peroxide is completed, the materials in the reactor are kept insulated and stirred for 2 hours. After separation, washing and dehydration, 501kg of epoxy intermediate product (epoxy fatty acid methyl ester) was obtained. The epoxidation process produces 102 kg of formic acid solution with a concentration of 40%.
[0033] Add the above-mentioned epoxy intermediate product to the chlorination re...
PUM
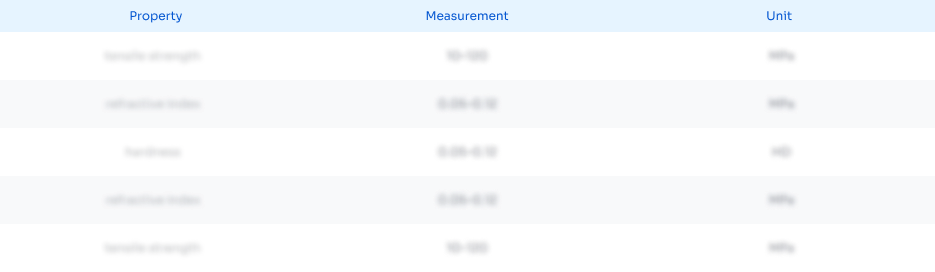
Abstract
Description
Claims
Application Information

- R&D
- Intellectual Property
- Life Sciences
- Materials
- Tech Scout
- Unparalleled Data Quality
- Higher Quality Content
- 60% Fewer Hallucinations
Browse by: Latest US Patents, China's latest patents, Technical Efficacy Thesaurus, Application Domain, Technology Topic, Popular Technical Reports.
© 2025 PatSnap. All rights reserved.Legal|Privacy policy|Modern Slavery Act Transparency Statement|Sitemap|About US| Contact US: help@patsnap.com