Three-component composite yarn and yarn forming method thereof
A composite yarn, three-component technology, applied in the field of fabric fibers, can solve the problems of low versatility of fabrics, no double elastic modulus, etc., and achieve the effect of improving fluffy effect and improving tightness.
- Summary
- Abstract
- Description
- Claims
- Application Information
AI Technical Summary
Problems solved by technology
Method used
Image
Examples
Embodiment
[0020] Example Manufacture of Composite Yarn
[0021] Combined with ZL02104397.3, on the FA506 ring spinning machine, the staple fiber strands as the outsourcing fibers are fed to the cradle drafting mechanism through the bell mouth of the machine for drafting, and the network yarns (PET DTY77dtex / 36f+PU 44dtex / 1f) is drawn out from the filament unwinding device, filament tension control device and filament positioning guide device, and then fed into the nip of the front roller from the rear of the front roller. twisting zone. Before entering the composite twisting zone, the tension of the filament is controlled by a specific tension device, so that the tension value of the filament is kept stable and within a reasonable range during spinning; at the same time, the filament is controlled by a positioning guide device to be aligned with the center of the staple fiber. Entering the twisting triangle area ensures the coaxial composite twisting of staple fiber strands and filamen...
PUM
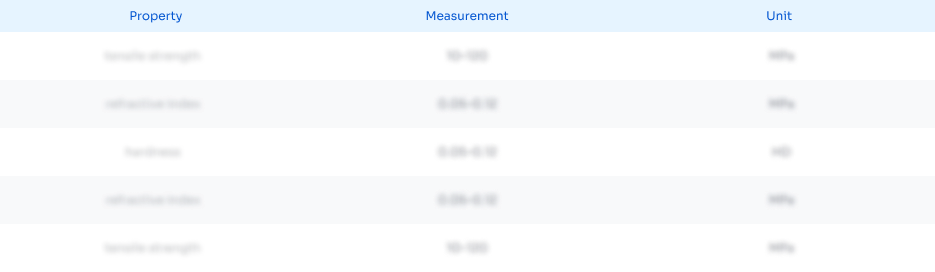
Abstract
Description
Claims
Application Information

- R&D Engineer
- R&D Manager
- IP Professional
- Industry Leading Data Capabilities
- Powerful AI technology
- Patent DNA Extraction
Browse by: Latest US Patents, China's latest patents, Technical Efficacy Thesaurus, Application Domain, Technology Topic, Popular Technical Reports.
© 2024 PatSnap. All rights reserved.Legal|Privacy policy|Modern Slavery Act Transparency Statement|Sitemap|About US| Contact US: help@patsnap.com