Combined process method for heavy oil modification
A combined process and heavy oil upgrading technology, which is applied in the petroleum industry, hydrotreating process, hydrocarbon oil treatment, etc., can solve the problem of reducing the processing capacity and economic benefits of heavy oil catalytic cracking units, increasing the sulfur content of products, and increasing the load of regenerators, etc. problems, to achieve the effect of improving the fusion effect and reaction effect, increasing the yield of light oil, and reducing the load
- Summary
- Abstract
- Description
- Claims
- Application Information
AI Technical Summary
Problems solved by technology
Method used
Image
Examples
Embodiment -1
[0021] After the Tahe residual oil is treated with the same filtration as the conventional process, the heavy oil raw material is subjected to supercritical treatment, and added to the static mixer with tetralin, (keep excess tetralin, the weight of heavy oil raw material and tetralin The ratio of oil to agent is 1:6), and then the material is heated, enters the CSTR (continuously stirred tank reactor), pressurizes, heats up and starts stirring, the speed is 800 rpm, pressurizes to 20MPa, heats up to 400°C, the reaction time for 3h. The reacted product enters the separator after being filtered, and the gas phase and liquid phase are separated. The solid impurities separated by filtration can be burned or used as needle coke raw materials, and the liquid phase enters the fractionation tower. The fractionation tower separates various light fractions (gasoline fraction and diesel fraction) and excess hydrogen-donating solvent. The excess hydrogen-donating solvent can be recycled...
Embodiment -2
[0023] Using Tahe residual oil as raw material, the supercritical treatment steps are the same as in Example-1. The heavy oil raw material is subjected to supercritical treatment, the hydrogen-donating solvent is decahydronaphthalene, the weight ratio of heavy oil raw material and hydrogen-donating solvent is 1:2, the reaction pressure is 35MPa, the reaction temperature is 450°C, and the reaction time is 0.5h (CSTR is a continuous feed discharge, the reaction time is the average residence time of the material). The heavy oil fraction separated from the fractionation tower enters catalytic cracking, the operating conditions are temperature 510°C, pressure 0.2MPa, solvent-oil ratio 5:1, space velocity 10h -1 . Separating the reaction products to obtain dry gas, liquefied petroleum gas, gasoline, diesel oil, heavy cycle oil and oil slurry, in which the heavy cycle oil is recycled to supercritical treatment; after the oil slurry is distilled to separate the residue, the distillat...
Embodiment -3
[0025] By the same method as in Example 2, water was added while using decahydronaphthalene, and the weight ratio of water and supercritical treatment feed was 2: 1. The catalytic cracking reaction results are shown in Table 2.
PUM
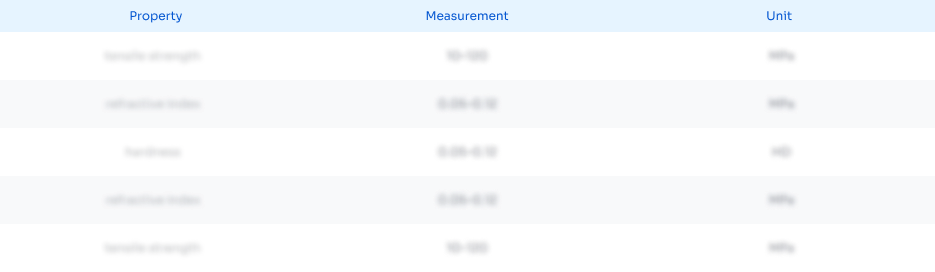
Abstract
Description
Claims
Application Information

- Generate Ideas
- Intellectual Property
- Life Sciences
- Materials
- Tech Scout
- Unparalleled Data Quality
- Higher Quality Content
- 60% Fewer Hallucinations
Browse by: Latest US Patents, China's latest patents, Technical Efficacy Thesaurus, Application Domain, Technology Topic, Popular Technical Reports.
© 2025 PatSnap. All rights reserved.Legal|Privacy policy|Modern Slavery Act Transparency Statement|Sitemap|About US| Contact US: help@patsnap.com