Heavy oil hydroprocessing method and reactor
A processing method, heavy oil hydrogenation technology, applied in the direction of processing hydrocarbon oil, chemical instruments and methods, petroleum industry, etc., can solve the problem of failure to achieve conversion and desulfurization, demetallization, increased equipment investment and operating costs, high conversion rate and Impurity removal rate and other issues, to achieve high impurity removal rate and conversion rate, slow down the severity of the operation, and good raw material adaptability
- Summary
- Abstract
- Description
- Claims
- Application Information
AI Technical Summary
Problems solved by technology
Method used
Image
Examples
Embodiment -1
[0044] According to the present invention, experiments were carried out on a 60L medium-sized plant. The diameter of the reactor is 160mm, the diameter of the sleeve is 80mm, the total height of the reactor is 3500mm, and the height of the sleeve is 2800. The loading capacity of the ebullating bed catalyst is 6L, which is a demetallization catalyst, and the particle size of the catalyst is 0.2mm. The fixed bed catalyst loading capacity in the annulus is 42L, which is also a demetallization catalyst. The properties and reaction results of the raw oil used are shown in Table 1, and the results of long-term operation are shown in Table 1. image 3 .
[0045] Table 1
[0046] category
[0047] From the reaction results in Table 1 and Figure 2-4 It can be seen from the operation curve that under the same conditions of reaction temperature, reaction pressure and total space velocity, the demetallization rate of the fixed bed process in Comparative Example-1 is almost ...
PUM
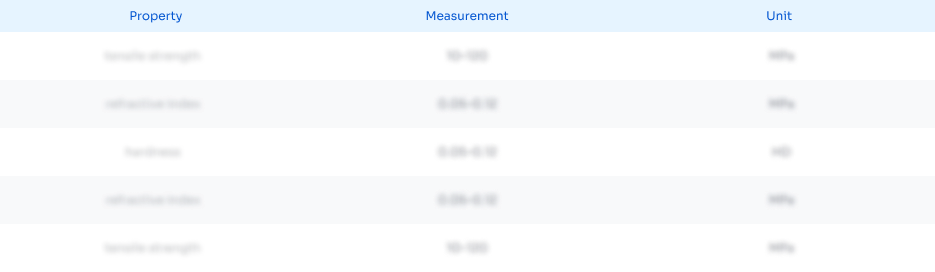
Abstract
Description
Claims
Application Information

- R&D
- Intellectual Property
- Life Sciences
- Materials
- Tech Scout
- Unparalleled Data Quality
- Higher Quality Content
- 60% Fewer Hallucinations
Browse by: Latest US Patents, China's latest patents, Technical Efficacy Thesaurus, Application Domain, Technology Topic, Popular Technical Reports.
© 2025 PatSnap. All rights reserved.Legal|Privacy policy|Modern Slavery Act Transparency Statement|Sitemap|About US| Contact US: help@patsnap.com