Method for preparing isooctanol polyoxyethylene polyoxypropylene ether phosphate ester
A technology of isooctyl alcohol polyoxyethylene polyoxypropylene ether phosphate and isooctyl alcohol polyoxyethylene polyoxypropylene ether is applied in the field of synthesis of anionic surfactants in organic chemistry, which can solve problems such as inconvenient production and operation, and achieve The effect of convenient production and operation, convenient operation and good permeability
- Summary
- Abstract
- Description
- Claims
- Application Information
AI Technical Summary
Problems solved by technology
Method used
Image
Examples
Embodiment 1
[0016] 170.0 g of isooctyl alcohol and 4.0 g of Mg-Al composite catalyst were added into a 2.5 L pressure reactor, and the ethylene oxide metering tank and the propylene oxide metering tank were respectively connected to the pressure reactor. Replace the air with nitrogen for 3 times, wait until the temperature of the kettle rises to 135-140° C., keep the system pressure at 0.2-0.3 MPa, start feeding 115.1 g of ethylene oxide, and continue the reaction for 0.5 hours after passing through for 2.0 hours. Begin to feed 75.8g propylene oxide then, pass through in 2.0 hours, continue reaction 1.5 hours. After the reaction is complete, cool, release the pressure, and filter. Move the obtained product into a 1000mL four-neck flask, add 53.1g of phosphorus pentoxide in batches, react at a temperature of 65-70°C for 4.5 hours, then add 2.1g of deionized water, and hydrolyze at a temperature of 80-85°C for 1.0 hour , cooled to obtain a colorless to pale yellow viscous liquid.
[0017]...
Embodiment 2
[0019] 350.0 g of isooctyl alcohol and 1.7 g of Mg-Al composite catalyst were added into a 2.5 L pressure reactor, and the ethylene oxide metering tank and the propylene oxide metering tank were respectively connected to the pressure reactor. Replace the air with nitrogen for 3 times, wait until the temperature of the kettle rises to 175-180°C, keep the system pressure at 0.2-0.3MPa, start feeding 355.4g of ethylene oxide for 2.5 hours, and continue the reaction for 1.0 hour. Begin to feed 156.2g propylene oxide then, pass through in 2.0 hours, continue to react for 2.0 hours. After the reaction is complete, cool, release the pressure, and filter. Move the obtained product into a 1000mL four-neck flask, add 139.0g of phosphorus pentoxide in batches, react at a temperature of 70-75°C for 4.0 hours, then add 20.0g of deionized water, and hydrolyze at a temperature of 70-80°C for 1.5 hours , cooled to obtain a colorless to pale yellow viscous liquid.
[0020] Wherein the prepar...
Embodiment 3
[0022] 235.0 g of isooctyl alcohol and 12.1 g of Mg-Al composite catalyst were added into a 2.5 L pressure reactor, and the ethylene oxide metering tank and the propylene oxide metering tank were respectively connected to the pressure reactor. Replace the air with nitrogen for 3 times, wait until the temperature of the kettle rises to 70-75°C, keep the system pressure at 0.2-0.3MPa, start to feed 159.1g of ethylene oxide, complete the passage in 2.0 hours, and continue the reaction for 1.0 hour. Then start to feed 209.7g propylene oxide, pass through in 3.0 hours, continue to react for 2.5 hours. After the reaction is complete, cool, release the pressure, and filter. Move the obtained product into a 1000mL four-neck flask, add 128.3g of phosphorus pentoxide in batches, react at a temperature of 60-65°C for 3.5 hours, then add 7.3g of deionized water, and hydrolyze at a temperature of 60-65°C for 1.5 hours , cooled to obtain a colorless to pale yellow viscous liquid.
[0023]...
PUM
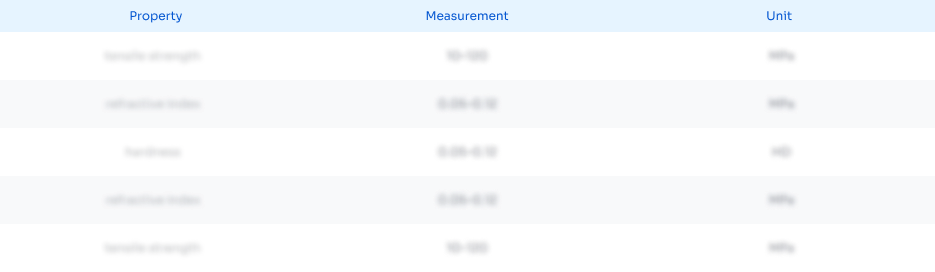
Abstract
Description
Claims
Application Information

- R&D
- Intellectual Property
- Life Sciences
- Materials
- Tech Scout
- Unparalleled Data Quality
- Higher Quality Content
- 60% Fewer Hallucinations
Browse by: Latest US Patents, China's latest patents, Technical Efficacy Thesaurus, Application Domain, Technology Topic, Popular Technical Reports.
© 2025 PatSnap. All rights reserved.Legal|Privacy policy|Modern Slavery Act Transparency Statement|Sitemap|About US| Contact US: help@patsnap.com