Method for preparing low-carbon olefine catalyst by loading iron-based synthetic gas
A technology for low-carbon olefins and synthesis gas, which is applied in catalyst activation/preparation, chemical instruments and methods, physical/chemical process catalysts, etc. The effect of high mechanical strength, improved activity, and simple preparation method
- Summary
- Abstract
- Description
- Claims
- Application Information
AI Technical Summary
Problems solved by technology
Method used
Image
Examples
example 1
[0018] Weigh commercially available silica gel (pore volume is 1.06ml / g, specific surface area is 386.81m 2 / g, the following examples all use the silica gel) 30g, distilled water is added dropwise to initial moistening, and the volume of consumed water is 48ml. The aqueous solution with a sucrose mass concentration of 5% was adjusted to a pH value of 3 with sulfuric acid, and the mass ratio of the silica gel to the mixed solution was 1:4, and the silica gel and the sucrose acidic solution were fully mixed and stirred for 2 hours at a temperature of 60°C. Dry at 60°C for 24 hours, and then bake at 800°C for 10 hours in vacuum or nitrogen atmosphere.
[0019] Based on the final catalyst K content of 0.03 wt%, 0.0234 g of potassium nitrate was weighed and dissolved in 48 ml, added to the modified carrier silica gel for impregnation, dried at 60° C. for 24 hours, and roasted at 350° C. in vacuum or nitrogen atmosphere for 10 hours. Based on the final catalyst Fe content of 4wt%,...
example 2
[0022] Weigh commercially available silica gel, add distilled water dropwise until initial moistening, and the volume of consumed water is 48ml. The aqueous solution with a sucrose mass concentration of 15% was adjusted to a pH value of 2 with hydrochloric acid, and the mass ratio of the silica gel to the mixed solution was 1:9, and the silica gel and the sucrose acidic solution were fully mixed and stirred at a temperature of 70° C. for 3.5 hours. Dry at 100°C for 16 hours, then vacuum bake at 900°C for 8 hours.
[0023] Based on the final catalyst K content of 0.25 wt%, 0.1939 g of potassium nitrate was weighed and dissolved in 48 ml, added to the above-mentioned modified carrier silica gel for impregnation, dried at 100 ° C for 16 hours, and roasted in vacuum or nitrogen atmosphere at 550 ° C for 4 hours. Based on the final catalyst Fe content of 6wt%, 13.0212g of iron nitrate was weighed and dissolved in 48ml, added to the above-mentioned potassium-impregnated sample, drie...
example 3
[0025]Weigh commercially available silica gel, add distilled water dropwise until initial moistening, and the volume of consumed water is 48ml. The aqueous solution with a sucrose mass concentration of 20% was adjusted to a pH value of 1 with sulfuric acid, and the mass ratio of the silica gel to the mixed solution was 1:12, and the silica gel and the sucrose acidic solution were fully mixed and stirred for 5 hours at a temperature of 80°C. Dry at 120°C for 8 hours, then vacuum bake at 1000°C for 4 hours.
[0026] Based on the final catalyst K content of 0.53 wt%, 0.1939 g of potassium nitrate was weighed and dissolved in 48 ml, added to the above-mentioned modified carrier silica gel for impregnation, dried at 150 ° C for 8 hours, and roasted in vacuum or nitrogen atmosphere at 700 ° C for 2 hours. Based on the final catalyst Fe content of 8wt%, 17.3616g of ferric nitrate was weighed and dissolved in 48ml, added to the above-mentioned sample impregnated with potassium, dried ...
PUM
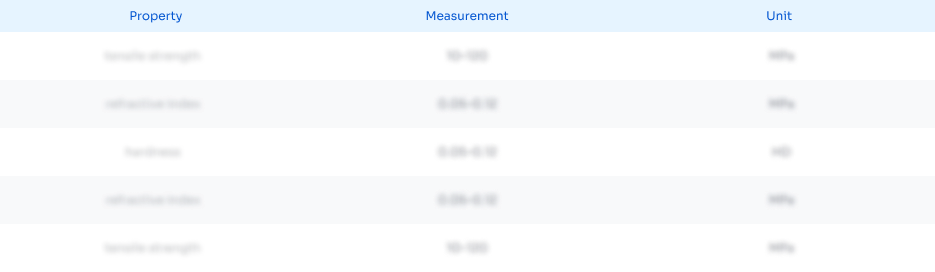
Abstract
Description
Claims
Application Information

- R&D
- Intellectual Property
- Life Sciences
- Materials
- Tech Scout
- Unparalleled Data Quality
- Higher Quality Content
- 60% Fewer Hallucinations
Browse by: Latest US Patents, China's latest patents, Technical Efficacy Thesaurus, Application Domain, Technology Topic, Popular Technical Reports.
© 2025 PatSnap. All rights reserved.Legal|Privacy policy|Modern Slavery Act Transparency Statement|Sitemap|About US| Contact US: help@patsnap.com