Lithium ion battery grouping method
A lithium-ion battery, battery technology, applied in non-aqueous electrolyte battery, electrolyte battery manufacturing, secondary battery repair/maintenance, etc., can solve the problem of less than optimal battery efficiency
- Summary
- Abstract
- Description
- Claims
- Application Information
AI Technical Summary
Problems solved by technology
Method used
Image
Examples
Embodiment 1
[0023] Matching method of the present invention, through the following steps to 002 # Box battery for matching:
[0024] 1. Select the battery cells with the same capacity range whose difference is less than 0.1Ah, in this case, 002 with 5.3Ah~5.4Ah # Box of 35 batteries.
[0025] 2. Leave the batteries after binning for at least 72 hours, 002 # The date of capacity division of the box battery is July 15, 2010, and the date of grouping is July 21, 2010. It has been put on hold for 6 days and meets the requirements.
[0026] 3. Connect the batteries with the same capacity in series according to the number required for each group, and connect 10 batteries in series with battery clips.
[0027] 4. Connect a voltmeter to each battery in parallel. For the convenience of recording, the battery cells are numbered from No. 1 to No. 10 from the total negative terminal of the battery pack. The recorded data is shown in Record Table 1. It can be seen from the table that the open circu...
Embodiment 2
[0035] Test and compare IMPDG211005001 and IMPDG211005002 to verify the superiority of the grouping method of the present invention. Battery pack capacity test:
[0036] Table 2 Capacity Test Record Form
[0037] Test parameters
[0038] It can be seen from the table that the batteries assembled by the method of the present invention have significantly higher capacity than batteries of the same specification by other assembly methods when discharging at high current.
[0039] Terminal voltage at the end of discharge of the battery pack:
[0040] Table 3 terminal voltage test record table
[0041] Test parameters
[0042] 1A charge 15A discharge
[0043] It can be seen from the table that the discharge cut-off voltage of the batteries assembled by the method of the present invention is lower than that of batteries with the same specifications of batteries assembled by other methods, indicating that the battery pack has a larger discharge depth an...
PUM
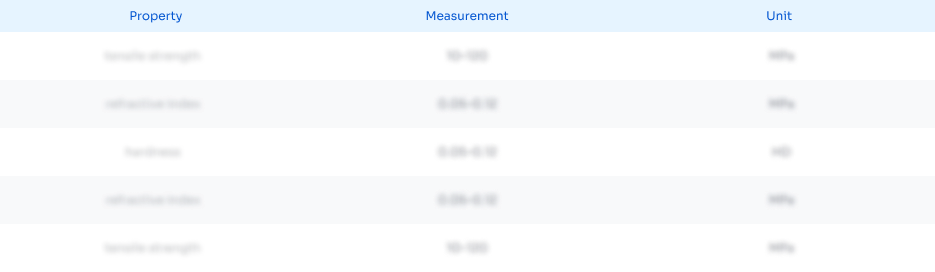
Abstract
Description
Claims
Application Information

- Generate Ideas
- Intellectual Property
- Life Sciences
- Materials
- Tech Scout
- Unparalleled Data Quality
- Higher Quality Content
- 60% Fewer Hallucinations
Browse by: Latest US Patents, China's latest patents, Technical Efficacy Thesaurus, Application Domain, Technology Topic, Popular Technical Reports.
© 2025 PatSnap. All rights reserved.Legal|Privacy policy|Modern Slavery Act Transparency Statement|Sitemap|About US| Contact US: help@patsnap.com