Incineration fly ash cement kiln synergic processing process
A technology of fly ash incineration and co-processing, applied in cement production and other directions, can solve problems such as improper disposal of heavy metals, and achieve the effect of avoiding high energy consumption
- Summary
- Abstract
- Description
- Claims
- Application Information
AI Technical Summary
Problems solved by technology
Method used
Image
Examples
Embodiment 1
[0021] The incineration fly ash of a circulating fluidized bed in a municipal solid waste incineration plant, the element content of Cl is 3.20wt%, Al 2 o 3 , CaO, SiO 2 , the contents are respectively 23.19%, 10.95%, 42.22%, accounting for 76.36% of the total.
[0022] Mix about 1 ton of fly ash and water in each batch according to the mass ratio of water-cement ratio of 3:1 in 1# washing kettle, and send the ash-water mixture into 1# belt filter press with slurry pump after 10 minutes The fly ash filter cake is obtained by dehydration, and the fly ash filter cake is sent to the 2# washing tank by the conveyor belt for the second washing operation with the same process parameters, and then the ash-water mixture is sent to the 2# belt filter press with the slurry pump Dehydration, the filtrate of 2# belt filter press is circulated for the washing process of 1# washing kettle, and the fly ash filter cake is sent to the 3# washing kettle through the conveyor belt for the third...
Embodiment 2
[0024] Fly ash and water are mixed and stirred in the washing kettle according to the mass ratio of water-cement ratio 10:1, washed with water for about 10 minutes, and then left to settle for half an hour, so that the supernatant overflows to the waste water treatment tank; then add clean water to the washing kettle to The original water-cement ratio, after stirring and washing for about 5 minutes, use the slurry pump to send the gray-water mixture into the plate-and-frame filter press to obtain the fly ash filter cake. The moisture content of the fly ash filter cake is 30%, and the chlorine element content down to 0.52wt%. The washing wastewater is passed into the tail gas of the cement kiln flue for acidification treatment, and when the pH value reaches 6-9, a flocculant is added and stirred for 5 minutes, and then the flocculation and sedimentation treatment is carried out to obtain the wastewater treatment sediment. Fly ash filter cake and wastewater treatment sediment ar...
PUM
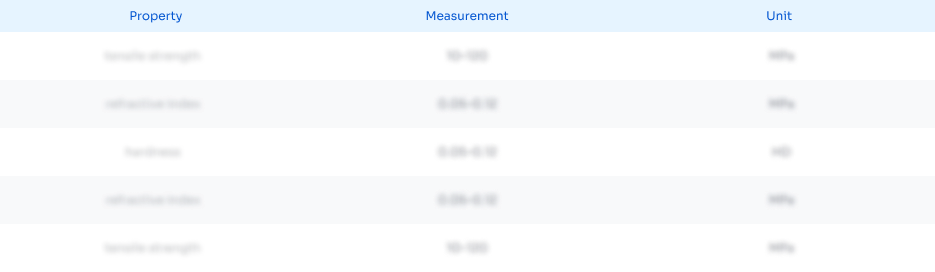
Abstract
Description
Claims
Application Information

- R&D
- Intellectual Property
- Life Sciences
- Materials
- Tech Scout
- Unparalleled Data Quality
- Higher Quality Content
- 60% Fewer Hallucinations
Browse by: Latest US Patents, China's latest patents, Technical Efficacy Thesaurus, Application Domain, Technology Topic, Popular Technical Reports.
© 2025 PatSnap. All rights reserved.Legal|Privacy policy|Modern Slavery Act Transparency Statement|Sitemap|About US| Contact US: help@patsnap.com