Steam-cleaning free printing process for disperse dye
A technology of disperse dyes and printing process, applied in the direction of dyeing method, textile and papermaking, adhesive type, etc., can solve the problems of fresh water waste, environmental pollution, ecological environment damage, etc., to achieve good fluidity, mature technology, printing low cost effect
- Summary
- Abstract
- Description
- Claims
- Application Information
AI Technical Summary
Problems solved by technology
Method used
Image
Examples
Embodiment 1
[0055] Example 1 Flat screen machine printing process of disperse dyes without steaming and washing
[0056] Such as figure 1 As shown, in this embodiment, the printing process verification is carried out by taking the printed fabric white brocade polyester twill jeanette as an example, and the specific process is as follows:
[0057] (1) Use the pre-configured disperse dye non-steaming printing paste and disperse dye to print on the refined white brocade polyester twill jeanette through the screen printing process of the flat screen printing machine;
[0058] Flat screen printing process parameters are as follows:
[0059] Printing dye: disperse dye; printing fabric: refined white brocade polyester twill jeanette; fabric width: 152 cm; guide material: oily resin sizing; platen temperature: room temperature; scraper specification: rubber flat knife; silk mesh Quantity: 120 mesh; Printing method: direct printing; Printing color registration: two colors with bottom (one color ...
Embodiment 2
[0072] Example 2 Rotary screen printing machine disperse dyes non-steaming and washing printing process
[0073] Such as figure 2 As shown, in this embodiment, the polyester satin cloth that has been softened is taken as an example to verify the non-steaming and washing printing process of disperse dyes. The specific process is as follows:
[0074] (1) Use the pre-configured disperse dye non-steaming printing paste and disperse dye to print on the softened polyester satin cloth through the screen printing process of the rotary screen printing machine;
[0075] The process is: polyester satin cloth that has been softened-screen printing-initial drying-styling, hair color synchronization-finishing, packaging and printing finished products. The specific parameters of the process are as follows: fabric pattern width: 152 cm; guide belt material: oleoresin sizing; platen temperature: room temperature; magnetic rod specification: 10; circular mesh: 125; printing method: direct pri...
Embodiment 3
[0079] Embodiment 3 Manual printing process
[0080] Such as image 3 As shown, this embodiment takes the whitening polyester satin jeanette as an example to verify the printing process, and the specific process is as follows:
[0081] (1) Use pre-configured disperse dye non-steaming printing paste and disperse dye to print on the softened polyester satin cloth through manual printing process;
[0082] The manual printing process parameters are as follows:
[0083] Using printing toner, disperse dye toner, pigment toner, printing fabric: whitening polyester satin jeanette, fabric width: 152 cm, platen resin: water-soluble platen glue, platen temperature: room temperature, Squeegee type: Resin bevel 45 degree knife, Screen mesh: 100 mesh, Printing method: Direct printing, Printing color: Three colors with bottom (two kinds of toner on whitening polyester jeanette), baking temperature : Natural drying, styling and hair color synchronization, synchronization speed: 40m / minute,...
PUM
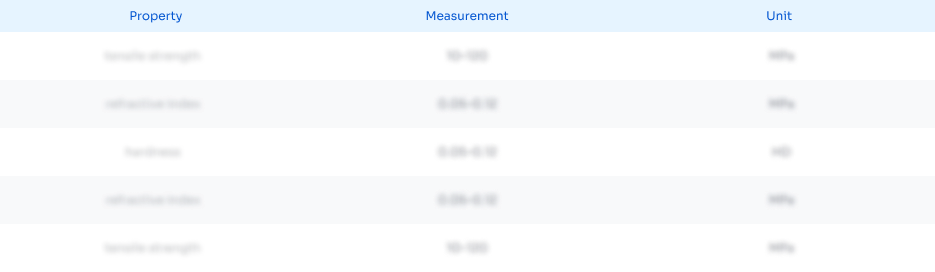
Abstract
Description
Claims
Application Information

- R&D Engineer
- R&D Manager
- IP Professional
- Industry Leading Data Capabilities
- Powerful AI technology
- Patent DNA Extraction
Browse by: Latest US Patents, China's latest patents, Technical Efficacy Thesaurus, Application Domain, Technology Topic, Popular Technical Reports.
© 2024 PatSnap. All rights reserved.Legal|Privacy policy|Modern Slavery Act Transparency Statement|Sitemap|About US| Contact US: help@patsnap.com