Production method of polytetrafluoroethylene granular powder
The technology of polytetrafluoroethylene micropowder and polytetrafluoroethylene is applied in the manufacturing field of polytetrafluoroethylene granular powder, which can solve the problems of entrained organic solvent, reduced product performance and high energy consumption.
- Summary
- Abstract
- Description
- Claims
- Application Information
AI Technical Summary
Problems solved by technology
Method used
Examples
Embodiment 1
[0055] In a 0.15M equipped with a conical belt stirrer 3 At the collection port of the mixer, quantitatively and continuously collect 70Kg of 10°C polytetrafluoroethylene powder from fluidized bed jet milling, the collection speed is 400Kg per hour, and the average particle size of polytetrafluoroethylene powder is 20μm. Polytetrafluoroethylene micropowder and 10 liters of synchronously atomized trichlorethylene are collected at the cylindrical collection port of the mixer (with 4 uniformly distributed nozzles at an elevation angle of 60° from the horizontal, the pressure at the nozzle inlet is 0.3Mpa, and the solvent mist The particle size of the particles is 110 microns) and mix evenly, the mixing temperature is 14°C, after the mixing is completed, the agitator of the mixer is turned on, the stirring speed is 23rpm, and the stirring time is 5 minutes. In a 0.42M equipped with a stirrer 3 Add 230 liters of deionized water at 20°C into the granulation tank, add the premixed m...
Embodiment 2
[0057] In a 0.15M equipped with a conical belt stirrer 3 At the collection port of the mixer, quantitatively and continuously collect 70Kg of 10°C polytetrafluoroethylene powder from the fluidized bed airflow pulverization, the collection speed is 400Kg per hour, and the average particle size of the polytetrafluoroethylene powder is 20μm. Polytetrafluoroethylene micropowder and 20 liters of synchronously atomized trichlorethylene are placed in a cylindrical mixer (with 4 uniformly distributed nozzles at an elevation angle of 40° from the horizontal, the pressure at the nozzle inlet is 0.7Mpa, and the solvent mist particles The particle size is 110 microns) and the collection port is uniformly mixed, and the mixing temperature is 15° C. After the mixing is completed, the agitator of the mixer is turned on, the stirring speed is 23 rpm, and the stirring time is 8 minutes. In a 0.42M equipped with a stirrer 3 Add 260 liters of deionized water at 21°C into the granulation tank, a...
Embodiment 3
[0059] In a 0.15M equipped with a conical belt stirrer 3 At the collection port of the mixer, quantitatively and continuously collect 70Kg of 10°C polytetrafluoroethylene powder from the fluidized bed airflow pulverization, the collection speed is 400Kg per hour, and the average particle size of the polytetrafluoroethylene powder is 20μm. Polytetrafluoroethylene micropowder and 30 liters of synchronously atomized trichlorethylene are collected at the cylindrical collection port of the mixer (with 4 uniformly distributed nozzles at an elevation angle of 60° from the horizontal, the pressure at the nozzle inlet is 0.7Mpa, and the solvent mist The particle size of the particles is 120 microns) and mix uniformly, and the mixing temperature is 17° C. After the mixing is completed, the agitator of the mixer is turned on, the stirring speed is 23 rpm, and the stirring time is 8 minutes. In a 0.42M equipped with a stirrer 3 Add 290 liters of deionized water at 20°C into the granulati...
PUM
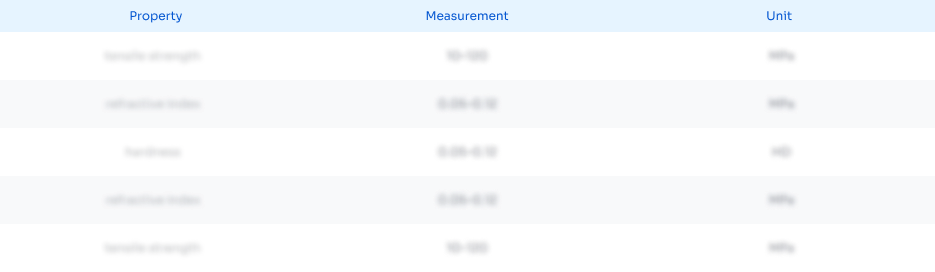
Abstract
Description
Claims
Application Information

- Generate Ideas
- Intellectual Property
- Life Sciences
- Materials
- Tech Scout
- Unparalleled Data Quality
- Higher Quality Content
- 60% Fewer Hallucinations
Browse by: Latest US Patents, China's latest patents, Technical Efficacy Thesaurus, Application Domain, Technology Topic, Popular Technical Reports.
© 2025 PatSnap. All rights reserved.Legal|Privacy policy|Modern Slavery Act Transparency Statement|Sitemap|About US| Contact US: help@patsnap.com