System adopting high concentration CO2 flue gas as coal dust drying medium in boiler
A drying medium and high-concentration technology, which is applied in the direction of drying gas arrangement, drying, drying machine, etc., can solve the problems of reducing the heat recovery of flue gas at the tail of the boiler, reducing the thermal efficiency of the boiler, and the impact of drying efficiency, so as to achieve faster moisture release , Complete combustion, fragile effect
- Summary
- Abstract
- Description
- Claims
- Application Information
AI Technical Summary
Problems solved by technology
Method used
Image
Examples
Embodiment Construction
[0017] The invention provides a boiler using high-concentration CO 2 The system in which flue gas is used as a coal powder drying medium will be further described below in conjunction with the accompanying drawings and specific embodiments.
[0018] Such as figure 1 As shown, the flue gas produced by boiler 1 fired with oxygen-enriched pulverized coal flows into economizer 2, the flue gas outlet of economizer 2 is connected to the flue gas inlet of dust collector 3, and the flue gas outlet of dust collector 3 is respectively connected to the boiler The recirculation flue gas inlet of 1 and the high-temperature flue gas inlet of gas-gas heat exchanger 6, the high-temperature flue gas outlet of gas-gas heat exchanger 6 are connected to the inlet of flue gas condenser 5, and the flue gas outlet of flue gas condenser 5 is connected to To the low-temperature flue gas inlet of the gas-gas heat exchanger 6, while the oxygen produced by the air separation device 4 is connected to the...
PUM
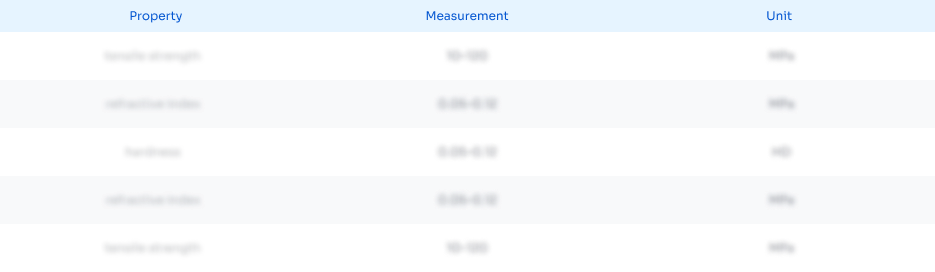
Abstract
Description
Claims
Application Information

- Generate Ideas
- Intellectual Property
- Life Sciences
- Materials
- Tech Scout
- Unparalleled Data Quality
- Higher Quality Content
- 60% Fewer Hallucinations
Browse by: Latest US Patents, China's latest patents, Technical Efficacy Thesaurus, Application Domain, Technology Topic, Popular Technical Reports.
© 2025 PatSnap. All rights reserved.Legal|Privacy policy|Modern Slavery Act Transparency Statement|Sitemap|About US| Contact US: help@patsnap.com