Preparation method of composite material based on epoxy resin and phosphazene nanotubes
A technology of epoxy resin and composite materials, which is applied in the field of nanomaterials, can solve the problems of loss of excellent properties, uneven dispersion, agglomeration, etc., achieve excellent heat resistance, good dielectric properties, and improve mechanical properties
- Summary
- Abstract
- Description
- Claims
- Application Information
AI Technical Summary
Problems solved by technology
Method used
Image
Examples
Embodiment 1
[0024] Step 1: Under 50W ultrasonic conditions, in a single-necked flask containing 10,000 parts by weight of tetrahydrofuran, add 87 parts by weight of triethylamine, then add 144 parts by weight of 4,4'-dihydroxydiphenyl sulfone and 50 parts by weight of Hexachlorocyclotriphosphazene reacted for 4 hours at 40 degrees Celsius, then added 900 parts by weight of epichlorohydrin, dripped 400 parts by weight of a 30% aqueous sodium hydroxide solution, and reacted in a water bath at 60 degrees Celsius for 4 hours, Wash with tetrahydrofuran, water and ethanol, filter, and dry to obtain epoxy group-modified phosphazene nanotubes with a yield of 83%.
[0025] Step 2 Add 8000 parts by weight of epoxy resin E618 to 6000 parts by weight of acetone, add 11 parts by weight of phosphazene nanotubes modified by epoxy groups, and then add 3000 parts by weight of 4,4'-di Aminodiphenylmethane, dispersed under the condition of ultrasonic 240W for 90 minutes, placed in a vacuum oven at 30 degree...
Embodiment 2
[0027] Step 1: Under 50W ultrasonic conditions, in a single-necked flask containing 20,000 parts by weight of tetrahydrofuran, add 174 parts by weight of triethylamine, then add 288 parts by weight of 4,4'-dihydroxydiphenyl sulfone and 100 parts by weight of Hexachlorocyclotriphosphazene reacted for 4 hours at 40 degrees Celsius, then added 1800 parts by weight of epichlorohydrin, dripped 800 parts by weight of 30% aqueous sodium hydroxide solution, and reacted in a water bath at 60 degrees Celsius for 6 hours, Wash with tetrahydrofuran, water and ethanol, filter, and dry to obtain epoxy group-modified phosphazene nanotubes with a yield of 78%.
[0028] Step 2 Add 8000 parts by weight of epoxy resin E618 to 5000 parts by weight of acetone, add 5.5 parts by weight of phosphazene nanotubes modified by epoxy groups, and then add 3000 parts by weight of 4,4'-bis Aminodiphenylmethane, dispersed under the condition of ultrasonic 240W for 90 minutes, placed in a vacuum oven at 30 deg...
Embodiment 3
[0030] Step 1 Under 50W ultrasonic conditions, in a single-necked flask containing 10000 parts by weight of tetrahydrofuran, add 174 parts by weight of triethylamine, then add 288 parts by weight of 4,4'-dihydroxydiphenyl sulfone and 100 parts by weight of Hexachlorocyclotriphosphazene reacted for 4 hours at 40 degrees Celsius, then added 1800 parts by weight of epichlorohydrin, dripped 800 parts by weight of 30% aqueous sodium hydroxide solution, and reacted for 4 hours in a water bath at 60 degrees Celsius. Wash with tetrahydrofuran, water and ethanol, filter, and dry to obtain epoxy group-modified phosphazene nanotubes with a yield of 81%.
[0031] Step 2 Add 8000 parts by weight of epoxy resin E618 to 8000 parts by weight of acetone, add 55 parts by weight of phosphazene nanotubes modified by epoxy groups, and then add 3000 parts by weight of 4,4'-di Aminodiphenylmethane, dispersed under the condition of ultrasonic 240W for 90 minutes, placed in a vacuum oven at 30 degrees...
PUM
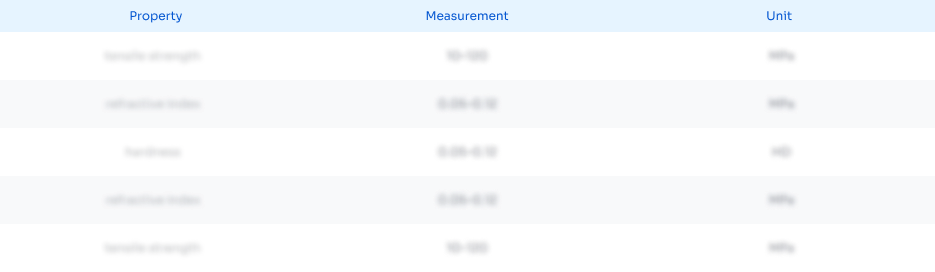
Abstract
Description
Claims
Application Information

- R&D
- Intellectual Property
- Life Sciences
- Materials
- Tech Scout
- Unparalleled Data Quality
- Higher Quality Content
- 60% Fewer Hallucinations
Browse by: Latest US Patents, China's latest patents, Technical Efficacy Thesaurus, Application Domain, Technology Topic, Popular Technical Reports.
© 2025 PatSnap. All rights reserved.Legal|Privacy policy|Modern Slavery Act Transparency Statement|Sitemap|About US| Contact US: help@patsnap.com