System control method based on maintenance type human-simulating PID
A control method and holding technology, applied to controllers with specific characteristics, electric controllers, etc., can solve problems such as frequent mutations in system control, large deviation signals, and system instability, etc., and achieve high promotion and application value, The effect of small overshoot and simple programming
- Summary
- Abstract
- Description
- Claims
- Application Information
AI Technical Summary
Problems solved by technology
Method used
Image
Examples
Embodiment 1
[0066] In this embodiment, the controlled variable y of the controlled object 3 is a liquid level parameter, the actuator 2 is a valve, the controlled object 3 is a liquid level tank, the measuring device 4 is a liquid level transmitter, and the PID Controllers, valves, level tanks and level transmitters form a complete level control system.
[0067] In the actual operation process, the control operation process of the PID controller in the liquid level control system is:
[0068] Step 1. Obtain the deviation signal e(t): Use the liquid level transmitter to detect the liquid level parameter y of the liquid level tank in real time, and simultaneously compare the detected signal r(t) with the set signal r through the difference comparator 0 (t) Compare the difference and get the liquid level deviation signal e(t), the obtained liquid level deviation signal e(t) is detailed in figure 2 ; The difference comparator synchronously transmits the liquid level deviation signal e(t) to...
Embodiment 2
[0093] In this embodiment, the difference from Embodiment 1 is that the controlled variable y of the controlled object 3 is a temperature parameter, the actuator 2 is a heater, the controlled object 3 is a constant temperature box, and the measuring device 4 is a temperature transmitter. controller, and the PID controller, heater, thermostat and temperature transmitter form a complete thermostat control system.
[0094] In the actual operation process, the control calculation process of the PID controller in the constant temperature control system is:
[0095] Step 1. Obtain the deviation signal e(t): Use a temperature transmitter to detect the temperature parameter y of the incubator in real time, and synchronously compare the detected signal r(t) with the set signal r through the difference comparator 0 (t) Comparing the difference and obtaining the temperature deviation signal e(t); the difference comparator synchronously transmits the liquid level deviation signal e(t) to ...
Embodiment 3
[0102] In this embodiment, the difference from Embodiment 1 is that the controlled variable y of the controlled object 3 is a voltage parameter, the actuator 2 is a switch control device, the controlled object 3 is a controllable voltage source, and the measuring device 4 is A voltage transmitter, and the PID controller, switch control device, controllable voltage source and voltage transmitter form a complete constant voltage control system.
[0103] In the actual operation process, the control operation process of the PID controller in the constant pressure control system is:
[0104] Step 1. Obtain the deviation signal e(t): Use a voltage transmitter to detect the voltage parameter y output by the controllable voltage source in real time, and synchronously compare the detected signal r(t) with the set signal through the difference comparator r 0 (t) performing difference comparison and obtaining a voltage deviation signal e(t); the difference comparator synchronously trans...
PUM
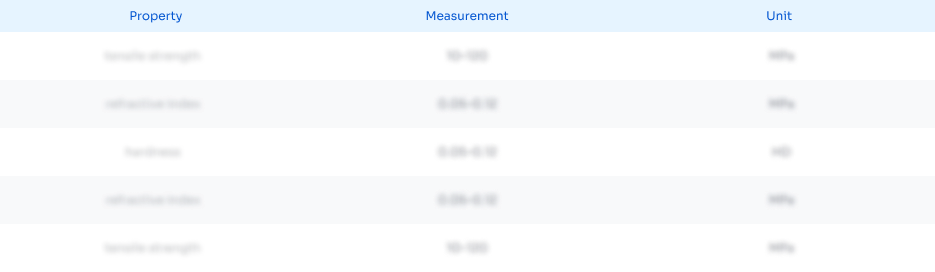
Abstract
Description
Claims
Application Information

- R&D
- Intellectual Property
- Life Sciences
- Materials
- Tech Scout
- Unparalleled Data Quality
- Higher Quality Content
- 60% Fewer Hallucinations
Browse by: Latest US Patents, China's latest patents, Technical Efficacy Thesaurus, Application Domain, Technology Topic, Popular Technical Reports.
© 2025 PatSnap. All rights reserved.Legal|Privacy policy|Modern Slavery Act Transparency Statement|Sitemap|About US| Contact US: help@patsnap.com