Process for preparing super-fine calcium sulfate from recycled sulfur dioxide waste gas
A technology of sulfur dioxide and calcium sulfate, which is applied in the fields of calcium/strontium/barium sulfate, chemical instruments and methods, and separation of dispersed particles, can solve problems such as sulfur dioxide pollution, and achieve the effect of reducing usage and production costs
- Summary
- Abstract
- Description
- Claims
- Application Information
AI Technical Summary
Problems solved by technology
Method used
Image
Examples
Embodiment
[0040] Take the production of 40 tons of dry process water glass per day as an example:
[0041] 1. Using sodium sulfate, silica sand, and reduced coal as raw materials, and industrial coal as fuel, heat-storage horseshoe furnace is used to produce water glass. The consumption of sodium sulfate is 0.95 tons / hour, the consumption of silica sand is 1.25 tons / hour, and the consumption of reduced coal is 0.10 tons / hour. After the material is evenly distributed, it is fed into the melting furnace at a feeding rate of 2.3 tons / hour. The flow rate of the molten water glass is 1.667 tons / hour, and the daily output of dry-process water glass is 40 tons.
[0042] 2. The temperature of the waste gas exiting the regenerative horseshoe water glass melting furnace is 320°C, the volume concentration of carbon dioxide is 3.1%, and the flow rate of the waste gas is 4736Nm / h
[0043] 3. The exhaust gas enters the absorption tower, and 25% sulfuric acid is formed in the absorption tower. The te...
PUM
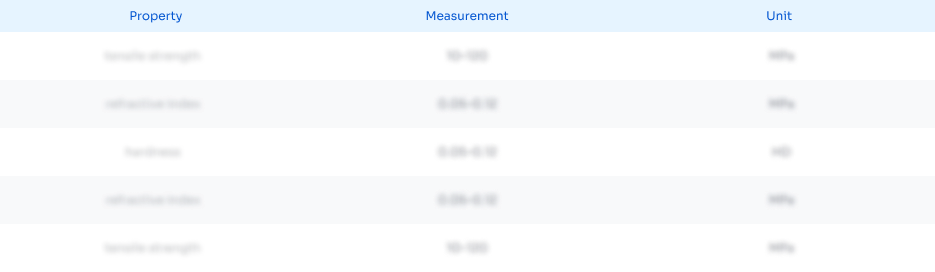
Abstract
Description
Claims
Application Information

- R&D Engineer
- R&D Manager
- IP Professional
- Industry Leading Data Capabilities
- Powerful AI technology
- Patent DNA Extraction
Browse by: Latest US Patents, China's latest patents, Technical Efficacy Thesaurus, Application Domain, Technology Topic, Popular Technical Reports.
© 2024 PatSnap. All rights reserved.Legal|Privacy policy|Modern Slavery Act Transparency Statement|Sitemap|About US| Contact US: help@patsnap.com