Method for melting glass
A glass and melting zone technology, applied in glass furnace equipment, glass manufacturing equipment, manufacturing tools, etc., can solve the problems of increased powder fuel consumption, reduced burner efficiency, and no formation of vanadium pentoxide and alumina
- Summary
- Abstract
- Description
- Claims
- Application Information
AI Technical Summary
Problems solved by technology
Method used
Image
Examples
Embodiment Construction
[0087] The present invention will be described below in conjunction with specific embodiments, wherein the same components will use the same reference numerals, figure 1 is a block diagram of an embodiment of the present invention, which mainly includes a system for supplying and burning pulverized fuel in at least one burner A of a side port glass melting furnace, which will be described later. The refractory device B of different shapes is used to form the wall, bottom and top of the glass melting furnace, the wall, bottom and top of the different combustion ports where the burner is arranged, and the wall, top and filler of the lattice body of the regenerator cavity, and the refractory The device is selected from silica, alumina, zircon, magnesite, chromium, ceramic, alumina-silicate, zircon-silicate, magnesia, or mixtures thereof. For example, the refractories are manufactured from: pressed silica, fused silica, direct cast silica; fusion cast alumina-silica-zircon; presse...
PUM
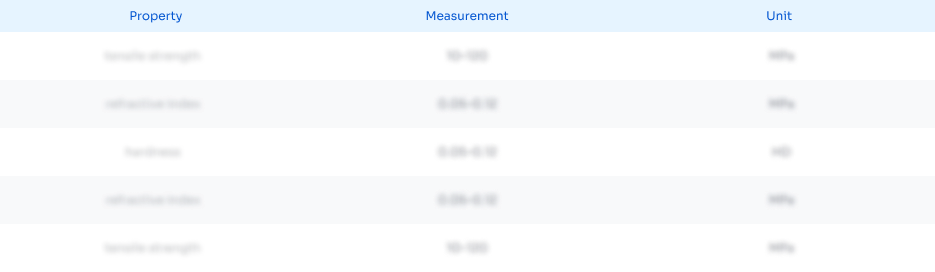
Abstract
Description
Claims
Application Information

- R&D
- Intellectual Property
- Life Sciences
- Materials
- Tech Scout
- Unparalleled Data Quality
- Higher Quality Content
- 60% Fewer Hallucinations
Browse by: Latest US Patents, China's latest patents, Technical Efficacy Thesaurus, Application Domain, Technology Topic, Popular Technical Reports.
© 2025 PatSnap. All rights reserved.Legal|Privacy policy|Modern Slavery Act Transparency Statement|Sitemap|About US| Contact US: help@patsnap.com