External combustion tube type direct reduction shaft furnace
A combustion tube type and direct technology, applied in the field of direct reduction of shaft furnaces, can solve the problems of influence of reduction effect, unsmooth connection, long construction time, etc., and achieve the effect of good reduction effect, good heating effect and stable heating effect.
- Summary
- Abstract
- Description
- Claims
- Application Information
AI Technical Summary
Benefits of technology
Problems solved by technology
Method used
Image
Examples
Embodiment 1
[0037] Such as Figure 1~3 In the shown external combustion tube type direct reduction shaft furnace, a plurality of reduction reaction tubes 2 are arranged in the furnace body 1, and the adjacent reduction reaction tubes 2 are arranged at intervals. The continuous area formed between the exterior of all the reduction reaction tubes 2 and the inner wall of the furnace body 1 is the combustion chamber 4 . Combustion chamber 4 adopts coal gas to ignite. Facilities such as the flue of combustion chamber 4 and the gas channel all can adopt existing structure, therefore do not show in the figure. With this arrangement, the surrounding area of each reduction reaction tube 2 is a high-temperature environment for combustion, so that the materials in each reduction reaction tube 2 are heated more uniformly and stably. Root reduction reaction tube 2, thus ensuring the unit capacity of the shaft furnace.
[0038] Wherein, a distributing device 8 is provided at the upper port 201 of ...
Embodiment 2
[0040] The difference between this embodiment 2 and embodiment 1 is that the structure of the distribution device 8 is different. Such as Figure 4 As shown, the distributing device 8 includes two inner and outer tubular members. Since the outer diameter of the inner tubular member is smaller than the inner diameter of the outer tubular member, an entry channel for the anti-sticking material is formed between the two tubular members. 804, and the lumen of the inner tubular member is the channel for the material undergoing the reduction reaction. Of course, the distributing device 8 still includes a discharger 802 and a discharger 803 for automatic supply of materials and release materials.
PUM
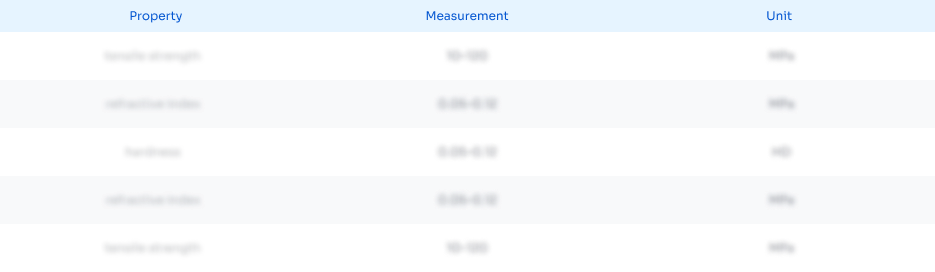
Abstract
Description
Claims
Application Information

- R&D
- Intellectual Property
- Life Sciences
- Materials
- Tech Scout
- Unparalleled Data Quality
- Higher Quality Content
- 60% Fewer Hallucinations
Browse by: Latest US Patents, China's latest patents, Technical Efficacy Thesaurus, Application Domain, Technology Topic, Popular Technical Reports.
© 2025 PatSnap. All rights reserved.Legal|Privacy policy|Modern Slavery Act Transparency Statement|Sitemap|About US| Contact US: help@patsnap.com