Ultrasonic bending fatigue experimental device
A technology of bending fatigue and experimental equipment, applied in the fields of durability testing and fatigue of structural materials, which can solve problems such as converting to transverse waves
- Summary
- Abstract
- Description
- Claims
- Application Information
AI Technical Summary
Problems solved by technology
Method used
Image
Examples
Embodiment Construction
[0051] This embodiment is an ultrasonic bending fatigue test device, which is used for a three-point bending fatigue test of metal materials at a frequency of 20 kHz, and can complete a bending fatigue test with a stress ratio R>0. According to the design of the connector and the low-magnification displacement amplifier in the ultrasonic bending fatigue test device, the stress amplitude loading range of the bending fatigue specimen is between 250-850 MPa. The ultrasonic bending fatigue specimen must meet the bending resonance condition of 20kHz, and the minimum length of the bending fatigue specimen should be greater than 30mm.
[0052] The ultrasonic bending fatigue test device includes a supporting device 4 , a bending fatigue sample 5 , a low-magnification displacement amplifier 6 , a connector 7 , a transducer 10 , a force transmitter, a static load adding device 13 , an isolation block 14 and an indenter 15 . The power transmission device is a frame structure composed of ...
PUM
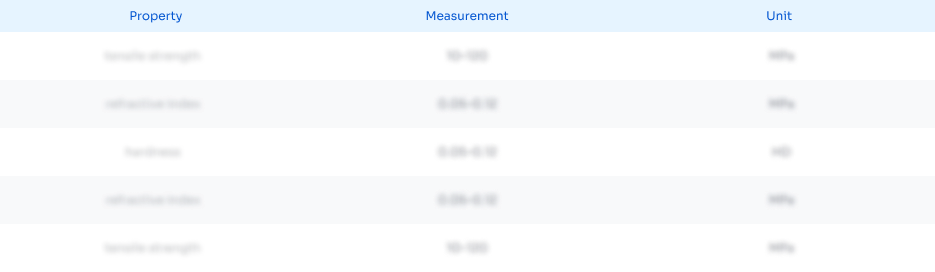
Abstract
Description
Claims
Application Information

- Generate Ideas
- Intellectual Property
- Life Sciences
- Materials
- Tech Scout
- Unparalleled Data Quality
- Higher Quality Content
- 60% Fewer Hallucinations
Browse by: Latest US Patents, China's latest patents, Technical Efficacy Thesaurus, Application Domain, Technology Topic, Popular Technical Reports.
© 2025 PatSnap. All rights reserved.Legal|Privacy policy|Modern Slavery Act Transparency Statement|Sitemap|About US| Contact US: help@patsnap.com