Method for preparing vanadium-aluminum alloy material
A vanadium-aluminum alloy material technology, applied in the field of alloy preparation, can solve the problems of high energy consumption, high vanadium-aluminum alloy impurity content, low smelting recovery rate, etc., and achieve the effect of reducing content and production energy consumption
- Summary
- Abstract
- Description
- Claims
- Application Information
AI Technical Summary
Problems solved by technology
Method used
Examples
Embodiment 1
[0007] By mass percentage, weigh the powdered Al 20%, V 2 O 5 50%, mixed in a ball mill for 8 hours, placed in a copper mold and compacted under a pressure of 60MPa with a press, put the mold containing the pressed reaction material in an aluminothermic reaction vessel, and placed on the material to ignite The residual air was blown out with an inert gas, and heated to about 300°C under the protection of 2MPa argon to obtain a vanadium-aluminum alloy with a mass percentage of vanadium of 75% and Al of 5.0%. In the prepared alloy, the mass fraction of vanadium is 83.855%, and the mass fraction of aluminum is 15.187%. The contents of other impurities are: Na: 0.063%, Si: 0.144%, S: 0.177%, Fe: 0.534%, Mo: 0.04%.
Embodiment 2
[0009] By mass percentage, weigh the powdered Al 26.5%, V 2 O 5 58.45%, after mixing in a ball mill for 12 hours, place it in a copper mold and compact it under a pressure of 70MPa with a press, place the mold containing the pressed reaction material in an aluminothermic reaction vessel, and place it on the material to ignite The residual air was blown out with an inert gas, and heated to about 300°C under the protection of 4MPa argon to obtain a vanadium-aluminum alloy with a mass percentage of vanadium of 85% and Al of 15.0%. In the prepared alloy, the mass fraction of vanadium is 86.117%, and the mass fraction of aluminum is 12.929%. The contents of other impurities are: Na: 0.059%, Si: 0.132%, S: 0.169%, Fe: 0.543%, Mo: 0.051%.
Embodiment 3
[0011] According to mass percentage, weigh the powdered Al 33.1%, V 2 O 5 66.9%, mixed in a ball mill for 16 hours, placed in a copper mold and compacted under a pressure of 80MPa with a press, put the mold containing the pressed reaction material in an aluminothermic reaction vessel, and placed on the material to ignite The residual air is blown out with an inert gas, and heated to about 300°C under the protection of 7MPa argon to obtain a vanadium-aluminum alloy with a mass percentage of vanadium of 95% and Al of 25.0%. In the prepared alloy, the mass fraction of vanadium is 89.996%, and the mass fraction of aluminum is 9.148%. The contents of other impurities are: Na: 0.053%, Si: 0.118%, S: 0.147%, Fe: 0.491
PUM
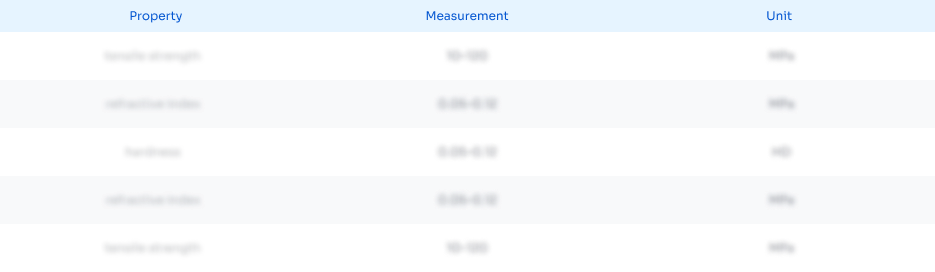
Abstract
Description
Claims
Application Information

- Generate Ideas
- Intellectual Property
- Life Sciences
- Materials
- Tech Scout
- Unparalleled Data Quality
- Higher Quality Content
- 60% Fewer Hallucinations
Browse by: Latest US Patents, China's latest patents, Technical Efficacy Thesaurus, Application Domain, Technology Topic, Popular Technical Reports.
© 2025 PatSnap. All rights reserved.Legal|Privacy policy|Modern Slavery Act Transparency Statement|Sitemap|About US| Contact US: help@patsnap.com