High temperature nylon PPA reinforcing material and preparation method thereof
A reinforcing material, nylon technology, applied in the field of high-temperature nylon PPA reinforced material and its preparation, can solve the problems of difficult processing and poor fluidity, and achieve the effects of simplified processing, broad application prospects, and reduced processing temperature
- Summary
- Abstract
- Description
- Claims
- Application Information
AI Technical Summary
Problems solved by technology
Method used
Examples
Embodiment 1
[0034] Take by weight 40 parts of polyphthalamide (PPA), 20 parts of polyamide (PA66), 10 parts of main flame retardant PBS-64HW, 4 parts of auxiliary flame retardant Sb2O3, 40 parts of long glass fiber 988A , antioxidants 1010 and 168 are 0.3 parts, lubricants TAF and siloxane are 0.3 parts, and nucleating agent CAV102 is 0.3 parts.
[0035] Composite materials were prepared by the following methods:
[0036]a. Weighing the raw materials and drying them respectively, including drying polyphthalamide (110°C for 3h) and polyamide (90°C for 4h);
[0037] b. Add the dried polyphthalamide and polyamide into the high-speed mixer, and add lubricant, nucleating agent and antioxidant, and mix at high speed for about 4 minutes;
[0038] c. Put the main flame retardant and auxiliary flame retardant into the high-speed mixer and mix for about 8 minutes. After mixing, add the mixed flame retardant to the previously mixed material and mix for about 6 minutes. Put the good material into t...
Embodiment 2
[0042] Weigh 35 parts of polyphthalamide (PPA), 10 parts of polyamide (PA66), 11.5 parts of main flame retardant PBS-64HW, 3.5 parts of auxiliary flame retardant Sb2O3, 40 parts of long glass fiber 988A by weight , antioxidants 1010 and 168 are 0.3 parts, lubricants TAF and siloxane are 0.3 parts, and nucleating agent CAV102 is 0.3 parts.
[0043] Composite materials were prepared by the following methods:
[0044] a. Weighing the raw materials, and drying the raw materials respectively, including drying polyphthalamide (120°C 3h) and polyamide (95°C 4h);
[0045] b. Add the dried polyphthalamide and polyamide into the high-speed mixer, and add lubricant, nucleating agent and antioxidant, and mix at high speed for about 4 minutes;
[0046] c. Put the main flame retardant and auxiliary flame retardant into the high-speed mixer and mix for about 7 minutes. After mixing, add the mixed flame retardant to the previously mixed material and mix for about 8 minutes. Put the good mat...
Embodiment 3
[0051] Weigh 34 parts of polyphthalamide (PPA), 9.5 parts of polyamide (PA66), 11.5 parts of main flame retardant PBS-64HW, 3.5 parts of auxiliary flame retardant Sb2O3, 40 parts of long glass fiber T635B , antioxidants 1010 and 168 are 0.3 parts, lubricants TAF and siloxane are 0.3 parts, and nucleating agent CAV102 is 0.3 parts.
[0052] Composite materials were prepared by the following methods:
[0053] a. Weighing the raw materials, and drying the raw materials respectively, including drying polyphthalamide (130°C 3h) and polyamide (100°C 4h);
[0054] b. Add the dried polyphthalamide and polyamide into the high-speed mixer, and add lubricant, nucleating agent and antioxidant, and mix at high speed for about 5 minutes;
[0055] c. Put the main flame retardant and auxiliary flame retardant into the high-speed mixer and mix for about 9 minutes. After mixing, add the mixed flame retardant to the previously mixed material and mix for about 5 minutes. Put the good material i...
PUM
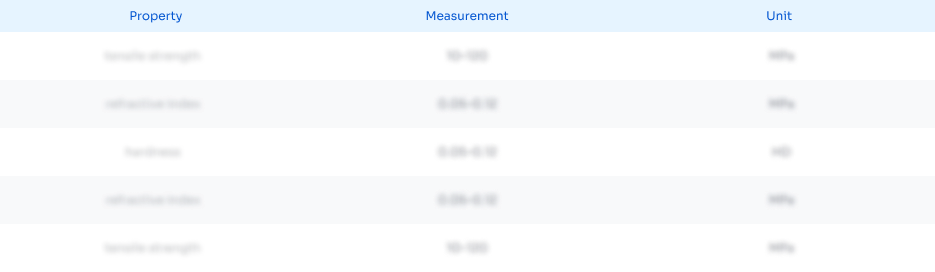
Abstract
Description
Claims
Application Information

- R&D
- Intellectual Property
- Life Sciences
- Materials
- Tech Scout
- Unparalleled Data Quality
- Higher Quality Content
- 60% Fewer Hallucinations
Browse by: Latest US Patents, China's latest patents, Technical Efficacy Thesaurus, Application Domain, Technology Topic, Popular Technical Reports.
© 2025 PatSnap. All rights reserved.Legal|Privacy policy|Modern Slavery Act Transparency Statement|Sitemap|About US| Contact US: help@patsnap.com