Short-flow casting and rolling composite forming method for ferrule piece
A composite forming and short-process technology, which is applied in the field of short-process casting-rolling composite forming of metal rings, can solve the problems of waste, waste of materials and energy, and achieve the effects of reducing waste, saving materials and labor
- Summary
- Abstract
- Description
- Claims
- Application Information
AI Technical Summary
Problems solved by technology
Method used
Examples
Embodiment 1
[0012] A short-flow casting-rolling composite forming method for metal rings in this embodiment, which includes alloy melting - molten steel refining - centrifugal casting ring blank - hot rolling expansion - rough machining - heat treatment - finishing Step: said molten steel refining refers to refining outside the ladle refining furnace (LF furnace), the smelting temperature is 1630°C-1650°C, blowing argon and stirring to quickly homogenize the composition and temperature of molten steel, reducing harmful impurities and gases in molten steel, During the refining process, alloys are added to the furnace to fine-tune the composition to obtain molten steel with high purity; the centrifugal casting ring billet refers to the centrifugal casting of the ring billet when the molten steel is refined at 1600 ° C, and at the same time, it is refined by electromagnetic stirring slab grains, reduce defects such as segregation of castings, improve equiaxed grain rate and slab quality; the ...
Embodiment 2
[0014] A short-flow casting-rolling composite forming method for metal rings in this embodiment, which includes alloy melting - molten steel refining - centrifugal casting ring blank - hot rolling expansion - rough machining - heat treatment - finishing Step: said molten steel refining refers to refining outside the ladle refining furnace (LF furnace), the smelting temperature is 1630°C-1650°C, blowing argon and stirring to quickly homogenize the composition and temperature of molten steel, reducing harmful impurities and gases in molten steel, During the refining process, the alloy is added into the furnace to fine-tune the composition to obtain molten steel with high purity; the centrifugal casting ring billet refers to the centrifugal casting of the ring billet when the molten steel is refined at 1600 ° C, and at the same time, it is refined by electromagnetic stirring slab grains, reduce defects such as segregation of castings, improve equiaxed grain rate and slab quality; ...
Embodiment 3
[0016] A short-flow casting-rolling composite forming method for metal rings in this embodiment, which includes alloy melting - molten steel refining - centrifugal casting ring blank - hot rolling expansion - rough machining - heat treatment - finishing Step: said molten steel refining refers to refining outside the ladle refining furnace (LF furnace), the smelting temperature is 1630°C-1650°C, blowing argon and stirring to quickly homogenize the composition and temperature of molten steel, reducing harmful impurities and gases in molten steel, During the refining process, the alloy is added into the furnace to fine-tune the composition to obtain molten steel with high purity; the centrifugal casting ring billet refers to the centrifugal casting of the ring billet when the molten steel is refined at 1600 ° C, and at the same time, it is refined by electromagnetic stirring slab grains, reduce casting segregation and other defects, improve equiaxed grain rate and slab quality; th...
PUM
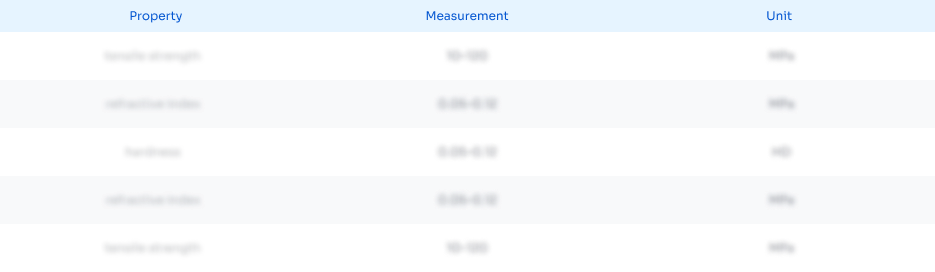
Abstract
Description
Claims
Application Information

- R&D
- Intellectual Property
- Life Sciences
- Materials
- Tech Scout
- Unparalleled Data Quality
- Higher Quality Content
- 60% Fewer Hallucinations
Browse by: Latest US Patents, China's latest patents, Technical Efficacy Thesaurus, Application Domain, Technology Topic, Popular Technical Reports.
© 2025 PatSnap. All rights reserved.Legal|Privacy policy|Modern Slavery Act Transparency Statement|Sitemap|About US| Contact US: help@patsnap.com