Bump air inlet method for realizing integration of unequal-strength wave system with forebody
A technology of air intake and front fuselage, which is applied in the field of bump air intake design, can solve the problems of not giving the selection principle of integrated design parameters, not paying attention to the integrated design of bump air intake, etc., so as to improve the air intake performance, increase the total pressure recovery coefficient curve, and reduce the effect of drag coefficient
- Summary
- Abstract
- Description
- Claims
- Application Information
AI Technical Summary
Problems solved by technology
Method used
Image
Examples
Embodiment Construction
[0040] The present invention will be described more fully below with reference to the accompanying drawings, each figure shows an application example of the present invention, and it should not be construed that the invention is limited to the application example described herein.
[0041] (1) Design of unequal strong wave system
[0042] figure 1 A schematic diagram of the wave system at the entrance of the Bump inlet of the present invention is shown. The supersonic incoming flow 1 generates a conical shock wave 3 at the head of the bulge compression surface 2, and forms a normal shock wave 5 in front of the inlet lip 4. Taking the design flow Mach number Ma=1.6 as an example, the two-wave system design of "conical shock wave + normal shock wave" is adopted, and the total pressure recovery coefficient of the inlet shock wave system is σ s = σ 1 ·σ 2 , where σ 1 , σ 2 are the total pressure recovery coefficients of the first and second shock waves respectively. Accordin...
PUM
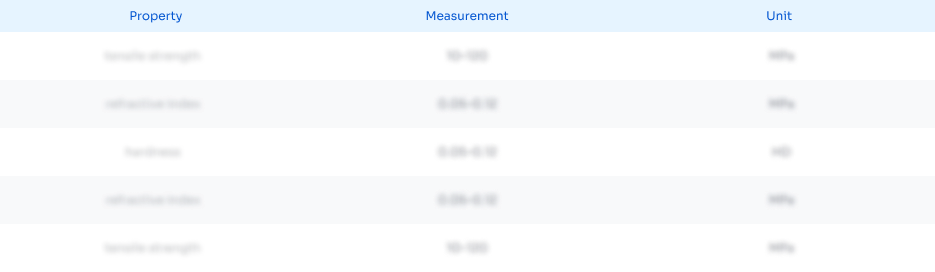
Abstract
Description
Claims
Application Information

- R&D
- Intellectual Property
- Life Sciences
- Materials
- Tech Scout
- Unparalleled Data Quality
- Higher Quality Content
- 60% Fewer Hallucinations
Browse by: Latest US Patents, China's latest patents, Technical Efficacy Thesaurus, Application Domain, Technology Topic, Popular Technical Reports.
© 2025 PatSnap. All rights reserved.Legal|Privacy policy|Modern Slavery Act Transparency Statement|Sitemap|About US| Contact US: help@patsnap.com