Production technology of cotton wool yarn dyed fabric
A production process, yarn-dyed technology, applied in the direction of fabric, weaving, dyeing, etc., can solve the problems of difficulty in dyeing process, great difference in physical properties of pure cotton and wool, etc., achieve smooth hand feeling, improve wearing performance, and broaden the market effect of space
- Summary
- Abstract
- Description
- Claims
- Application Information
AI Technical Summary
Problems solved by technology
Method used
Examples
Embodiment 1
[0012] The production process of wool-cotton yarn-dyed fabrics is as follows: After spinning wool and combed cotton yarn, it is produced through dyeing, warping, sizing, weaving, gray fabric inspection, singeing, desizing, shaping and pre-shrinking processes. Wool yarn-dyed fabrics, in the dyeing process, because wool is easily damaged under the high temperature of caustic soda, so non-alkali dyes and simultaneous dyeing process are used. The heating rate during the dyeing process is 0.4°C / min, which can be well The damage rate of wool is controlled to be less than 5%, the wool efficiency reaches 12.5-13cm / 30min, the degree index is about 5, the color flower is controlled at 0.2%, the level dyeing property of dyeing is greatly improved, and the dry and wet rubbing fastness of the yarn can reach 4 ~ Level 5 and above. In the spinning process, super-slip and wool oil are used as lubricants, mixed with water according to the ratio of 6:100 by mass percentage, and sprayed evenly o...
Embodiment 2
[0014] The production process of wool-cotton yarn-dyed fabrics is as follows: After spinning wool and combed cotton yarn, it is produced through dyeing, warping, sizing, weaving, gray fabric inspection, singeing, desizing, shaping and pre-shrinking processes. In the dyeing process of woolen cotton yarn-dyed fabrics, since wool is easily damaged under the high temperature of caustic soda, non-alkaline dyes and simultaneous dyeing processes are used. The heating rate during the dyeing process is 0.7°C / min, which can be well The damage rate of wool is controlled to be less than 5%, the wool efficiency reaches 12.5-13cm / 30min, the degree index is about 5, the color flower is controlled at 0.2%, the level dyeing property of dyeing is greatly improved, and the dry and wet rubbing fastness of the yarn can reach 4 ~ Level 5 and above. In the spinning process, super-slip and wool oil are used as lubricants, mixed with water at a ratio of 8:100 by mass percentage, and sprayed evenly on ...
Embodiment 3
[0016] The production process of wool-cotton yarn-dyed fabrics is as follows: After spinning wool and combed cotton yarn, it is produced through dyeing, warping, sizing, weaving, gray fabric inspection, singeing, desizing, shaping and pre-shrinking processes. Wool cotton yarn-dyed fabrics, in the dyeing process, because wool is easily damaged under the high temperature of caustic soda, so non-alkaline dyes and simultaneous dyeing process are used. The heating rate during the dyeing process is 0.6°C / min, which can be well The damage rate of wool is controlled to be less than 5%, the wool efficiency reaches 12.5-13cm / 30min, the degree index is about 5, the color flower is controlled at 0.2%, the level dyeing property of dyeing is greatly improved, and the dry and wet rubbing fastness of the yarn can reach 4 ~ Level 5 and above. In the spinning process, super-slip and wool oil are used as lubricants, mixed with water in a ratio of 7:100 by mass percentage, and sprayed evenly on t...
PUM
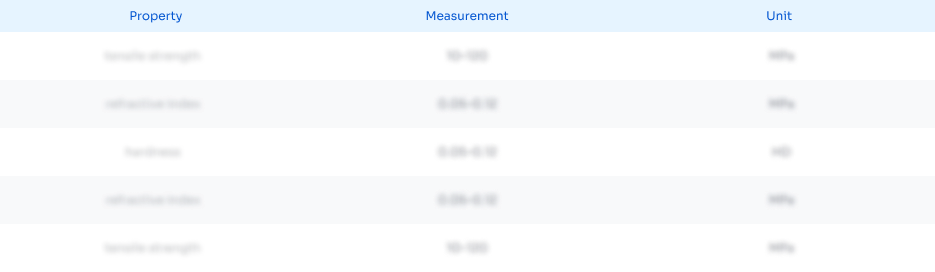
Abstract
Description
Claims
Application Information

- Generate Ideas
- Intellectual Property
- Life Sciences
- Materials
- Tech Scout
- Unparalleled Data Quality
- Higher Quality Content
- 60% Fewer Hallucinations
Browse by: Latest US Patents, China's latest patents, Technical Efficacy Thesaurus, Application Domain, Technology Topic, Popular Technical Reports.
© 2025 PatSnap. All rights reserved.Legal|Privacy policy|Modern Slavery Act Transparency Statement|Sitemap|About US| Contact US: help@patsnap.com