Method for manufacturing insulation layer of touch panel
A manufacturing method and touch panel technology, which are applied in the photoengraving process of pattern surface, semiconductor/solid-state device manufacturing, original parts for opto-mechanical processing, etc., can solve the problems of increased cost, complicated steps, dangerous processing process, etc. , to achieve the effect of improving yield, reducing costs, and reducing processing procedures
- Summary
- Abstract
- Description
- Claims
- Application Information
AI Technical Summary
Problems solved by technology
Method used
Image
Examples
Embodiment Construction
[0034] The above and other technical features and advantages of the present invention will be described in more detail below in conjunction with the accompanying drawings.
[0035] Figure 1-Figure 10 Shown are the schematic flow diagram of the present invention, the schematic diagrams of steps 1 to 8 of the present invention, and the schematic diagrams of another embodiment of the present invention. As shown in the figure: a method for manufacturing an insulating layer of a touch panel provided by the present invention can achieve the effects of reducing processing procedures, improving yield and reducing costs when manufacturing an insulating layer of a touch panel, which at least includes the following steps :
[0036] Step 1: Take a substrate 1 that can be a glass substrate or polyethylene terephthalate (PET), coat the first transparent conductive layer 2 on the substrate 1, and perform the first Second cleaning 10, wherein the first transparent conductive layer 2 is sel...
PUM
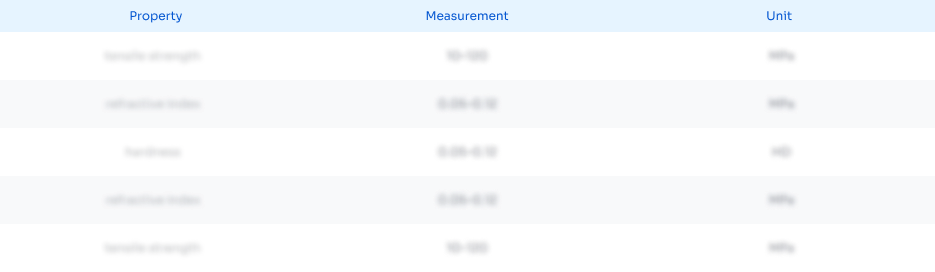
Abstract
Description
Claims
Application Information

- R&D
- Intellectual Property
- Life Sciences
- Materials
- Tech Scout
- Unparalleled Data Quality
- Higher Quality Content
- 60% Fewer Hallucinations
Browse by: Latest US Patents, China's latest patents, Technical Efficacy Thesaurus, Application Domain, Technology Topic, Popular Technical Reports.
© 2025 PatSnap. All rights reserved.Legal|Privacy policy|Modern Slavery Act Transparency Statement|Sitemap|About US| Contact US: help@patsnap.com