Dry flue gas desulphurization method using steel slag or blast furnace slag as absorbing agent
A dry flue gas desulfurization and blast furnace slag technology, applied in separation methods, chemical instruments and methods, dispersed particle separation, etc., can solve problems such as equipment corrosion, achieve small footprint, high system reliability, and save system occupation. earth effect
- Summary
- Abstract
- Description
- Claims
- Application Information
AI Technical Summary
Problems solved by technology
Method used
Examples
Embodiment 1
[0027] A boiler flue gas volume of 10000Nm 3 / h, sulfur dioxide content 800mg / Nm 3 , flue gas temperature 140 ℃. The flue gas desulfurization process of the present invention is used for desulfurization treatment, and the flue gas temperature at the outlet of the desulfurization tower is ≥70°C. Main chemical composition (mass ratio) of blast furnace slag: CaO (38.2%), SiO 2 (35.7%), Al 2 o 3 (16.3%), MgO (8.3%), S (1.01%).
[0028] The relevant operating parameters of this embodiment are as follows:
[0029] Process water consumption 320kg / h
[0030] Circular ash return 50kg / h
[0031] After treatment, the sulfur dioxide content is 120mg / Nm 3 , the desulfurization rate is 85%.
[0032] The specific process is as follows.
[0033] Select blast furnace slag with a particle size of ≤0.048mm, and spray the blast furnace slag into the desulfurization tower through the absorbent injection port by means of pneumatic conveying.
[0034] The clean process water is sprayed in...
Embodiment 2
[0040] A boiler flue gas volume of 110000Nm 3 / h, sulfur dioxide content 850mg / Nm 3, flue gas temperature 150 ℃. The flue gas desulfurization process of the present invention is used for desulfurization treatment, and the flue gas temperature at the outlet of the desulfurization tower is ≥70°C. Main chemical composition (mass ratio) of steel slag: CaO (54.92%), MgO (5.42%), total Fe (12.78%), S (1.62%).
[0041] The relevant operating parameters of this embodiment are as follows:
[0042] Process water consumption 3300kg / h
[0043] Circular ash return rate 600kg / h
[0044] After treatment, the sulfur dioxide content is 75mg / Nm 3 , the desulfurization rate is 91%.
[0045] The specific process is as follows.
[0046] Steel slag with particle size ≤0.048mm is selected, and the steel slag is sprayed into the desulfurization tower through the absorbent injection port by pneumatic conveying method.
[0047] The clean process water is sprayed into the desulfurization tower t...
Embodiment 3
[0053] A sintering flue gas volume of 200000Nm 3 / h, sulfur dioxide content 800mg / Nm 3 , flue gas temperature 110 ℃. The flue gas desulfurization process of the present invention is used for desulfurization treatment, and the flue gas temperature at the outlet of the desulfurization tower is ≥70°C. Main chemical composition (mass ratio) of steel slag: CaO (45.54%), MgO (9.42%), total Fe (11.43%), S (1.55%).
[0054] The relevant operating parameters of this embodiment are as follows:
[0055] Process water consumption 6100kg / h
[0056] Circular ash return 1000kg / h
[0057] After treatment, the sulfur dioxide content is 65mg / Nm 3 , the desulfurization rate is 92%.
[0058] The specific process is as follows.
[0059] Steel slag with particle size ≤0.048mm is selected, and the steel slag is sprayed into the desulfurization tower through the absorbent injection port by pneumatic conveying method.
[0060] The clean process water is sprayed into the desulfurization tower t...
PUM
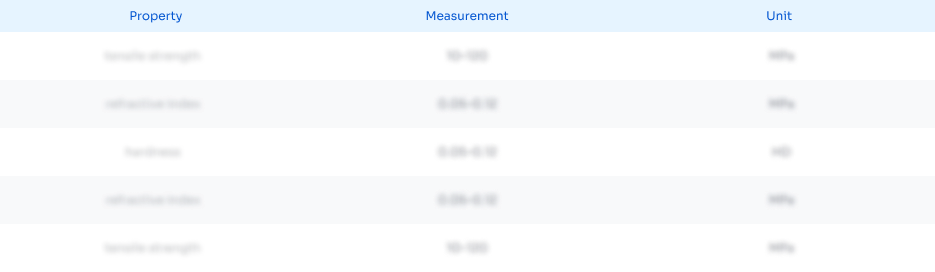
Abstract
Description
Claims
Application Information

- R&D
- Intellectual Property
- Life Sciences
- Materials
- Tech Scout
- Unparalleled Data Quality
- Higher Quality Content
- 60% Fewer Hallucinations
Browse by: Latest US Patents, China's latest patents, Technical Efficacy Thesaurus, Application Domain, Technology Topic, Popular Technical Reports.
© 2025 PatSnap. All rights reserved.Legal|Privacy policy|Modern Slavery Act Transparency Statement|Sitemap|About US| Contact US: help@patsnap.com