Tap hole integral pouring mud sleeve for blast furnace and manufacturing method thereof
An integral pouring and mud jacketing technology, applied in blast furnaces, blast furnace details, blast furnace parts, etc., can solve the problems of difficulty in production under pressure, long time consumption, and high consumption of refractory materials, so as to reduce the production workload and save money. Amount and cost, effect of reducing gas leakage
- Summary
- Abstract
- Description
- Claims
- Application Information
AI Technical Summary
Problems solved by technology
Method used
Image
Examples
Embodiment Construction
[0026] Depend on figure 1 , figure 2 It can be seen that the refractory castable 2 is poured into the mud sleeve frame 1 of the integral pouring mud sleeve of the iron gate fixed on the blast furnace shell 10 . The mud sleeve frame 1 is a box-shaped body, and the inside of the box plate 3 is provided with dovetail-shaped consolidation pendants 4 all over. The rear end of the mud jacket frame 1 is welded on the blast furnace shell 10 and surrounds the iron mouth; The module 7 is fixed on the formwork 6 and is aligned with the center of the iron hole. An iron pipe is set between the module 7 and the center of the iron hole, and the diameter of the iron pipe is equivalent to the diameter of the iron hole. Clay casing frame 1 is filled with castable 2, and after castable 2 is baked and consolidated, the iron pipe is melted, leaving a gap to drill iron channel 8.
[0027] The mud sleeve frame 1 is a steel plate structure, which can be used repeatedly for a long time; after the ...
PUM
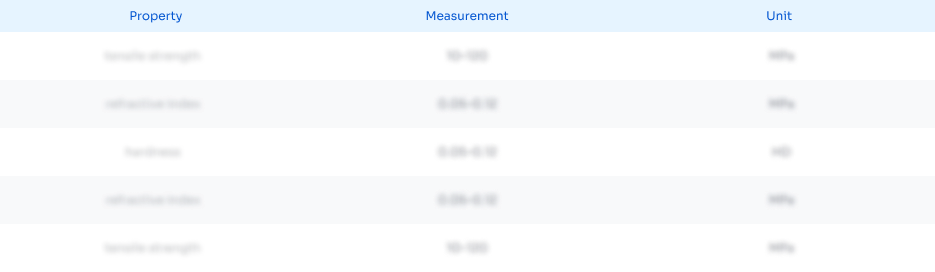
Abstract
Description
Claims
Application Information

- R&D
- Intellectual Property
- Life Sciences
- Materials
- Tech Scout
- Unparalleled Data Quality
- Higher Quality Content
- 60% Fewer Hallucinations
Browse by: Latest US Patents, China's latest patents, Technical Efficacy Thesaurus, Application Domain, Technology Topic, Popular Technical Reports.
© 2025 PatSnap. All rights reserved.Legal|Privacy policy|Modern Slavery Act Transparency Statement|Sitemap|About US| Contact US: help@patsnap.com