Ammonia-smoking method and flame-proof treatment method for pure cotton knitted fabric
A technology for flame retardant finishing, cotton knitted fabrics, applied in the direction of fabric surface trimming, heating/cooling fabrics, textile material processing, etc., can solve problems such as unsuitability of pure cotton fabrics
- Summary
- Abstract
- Description
- Claims
- Application Information
AI Technical Summary
Problems solved by technology
Method used
Image
Examples
Embodiment Construction
[0016] The flame retardant finishing method of pure cotton knitted fabric is as follows. First, the pure cotton knitted fabric is pad-rolled with a flame-retardant finishing solution containing a flame retardant through a sizing machine, and then the pure cotton knitted fabric is pre-dried at 100-120 ° C; Ammonia fumigated cross-linking room, so that the ammonia gas and the flame retardant on the knitted fabric are fully and evenly cross-linked; then oxidized, washed and dried. The flame-retardant effect of the pure cotton knitted fabric obtained through the flame-retardant finishing process of the present invention is uniform in the front, back, left, and right sides, and has no color flower problem.
[0017] see figure 1 , the upper and front parts of the ammonia fumigated crosslinking chamber 13 are provided with a steam inlet 4, the front part is also provided with a hatch 5 for entering the ammonia fumigated crosslinking chamber, and the rear part is provided with an amm...
PUM
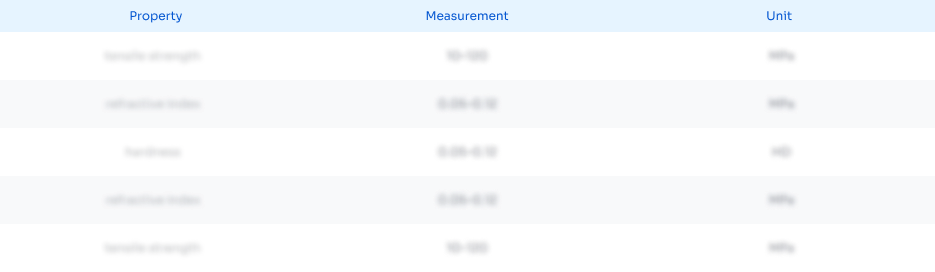
Abstract
Description
Claims
Application Information

- Generate Ideas
- Intellectual Property
- Life Sciences
- Materials
- Tech Scout
- Unparalleled Data Quality
- Higher Quality Content
- 60% Fewer Hallucinations
Browse by: Latest US Patents, China's latest patents, Technical Efficacy Thesaurus, Application Domain, Technology Topic, Popular Technical Reports.
© 2025 PatSnap. All rights reserved.Legal|Privacy policy|Modern Slavery Act Transparency Statement|Sitemap|About US| Contact US: help@patsnap.com