Continuous spinning process for viscose coarse denier flat filament
A spinning process and flat yarn technology, applied in the field of viscose filament production process, can solve the problems of unstable operation of the stranding machine, poor consistency, long process flow, etc., to reduce residual liquid in the previous process, reduce process fluctuation, The effect of shortening the process flow
- Summary
- Abstract
- Description
- Claims
- Application Information
AI Technical Summary
Problems solved by technology
Method used
Image
Examples
Embodiment Construction
[0023] The invention proposes a continuous spinning process for viscose thick denier flat yarn to overcome the disadvantages of the existing coarse denier flat yarn production process.
[0024] It is used for the continuous spinning process of viscose coarse denier flat yarn, including viscose metering molding, washing, drying and tube forming. The filaments formed in the pipe are drawn by the pinch rollers of the multi-stage washing tank to the washing tank for multi-stage washing. The filaments are dried, and then the dried filaments are formed into cylinders.
[0025] The multi-stage washing tank is connected front and back by multi-stage pressing rollers. The floor at the bottom of the washing tank is set as an inclined plane. The filaments pass through the first set of pressing rollers to reduce the residual liquid in the tube and enter the first-stage washing tank in a natural state. After soaking and washing in an orderly accumulation, guided by the glass guide wire ro...
PUM
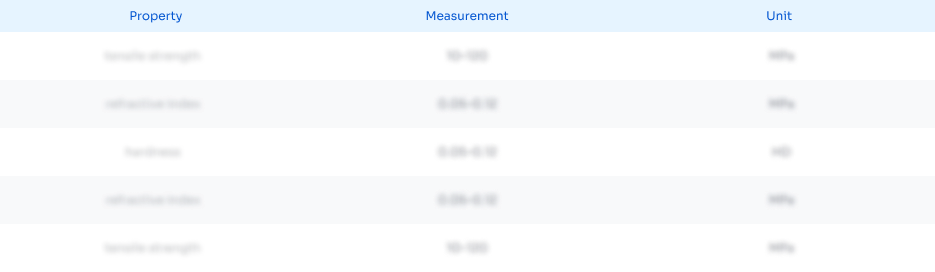
Abstract
Description
Claims
Application Information

- R&D
- Intellectual Property
- Life Sciences
- Materials
- Tech Scout
- Unparalleled Data Quality
- Higher Quality Content
- 60% Fewer Hallucinations
Browse by: Latest US Patents, China's latest patents, Technical Efficacy Thesaurus, Application Domain, Technology Topic, Popular Technical Reports.
© 2025 PatSnap. All rights reserved.Legal|Privacy policy|Modern Slavery Act Transparency Statement|Sitemap|About US| Contact US: help@patsnap.com