Full cyclodextrin polyrotaxane and preparation method thereof
A technology of cyclodextrin and polyrotaxane, which is applied in the field of full cyclodextrin polyrotaxane and its preparation, can solve the problem of low yield of polyrotaxane, and achieve fast end-capping reaction speed, high yield, and controllable strong effect
- Summary
- Abstract
- Description
- Claims
- Application Information
AI Technical Summary
Problems solved by technology
Method used
Image
Examples
Embodiment 1
[0018] At room temperature, a mixture of 100.0 mg of polyethylene glycol shaft chains containing alkyne bonds at the end (polyethylene glycol molecular weight is 4600 g / mol, containing 0.04 mmol of alkyne bonds) and 1.00 g of α-cyclodextrin (1.03 mmol) was dissolved in 10 mL In water, sonicate for 5 minutes and stir for 10 hours to form a pseudopolyrotaxane suspension; under the protection of nitrogen, 187.9 mg of azide monosubstituted β-cyclodextrin end-capping agent (0.16 mmol, the mole of azide and alkyne bond The ratio is 4:1), 40.5mg CuSO 4 ·5H 2 O (0.16mmol), 34.5μL 1,1,4,7,7-pentamethyldiethylenetriamine (0.16mmol) and 64.2mg sodium ascorbate (0.32mmol) were sequentially added to the pseudopolyrotaxane suspension , the mixture was reacted in the dark at room temperature for 2 hours, and the precipitate was collected by centrifugation. The precipitate was dissolved in DMSO and precipitated in water twice. The product was washed repeatedly with hot water at 50°C and drie...
Embodiment 2
[0020] Using the same reaction steps as in Example 1, the reaction time was 10 minutes, and the yield was 250 mg / 100 mg shaft chain.
Embodiment 3
[0022] Using the same reaction steps as in Example 1, the reaction time was 1 hour, and the yield was 280 mg / 100 mg shaft chain.
PUM
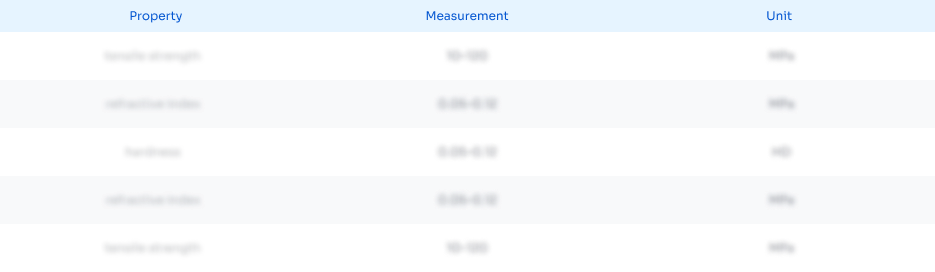
Abstract
Description
Claims
Application Information

- R&D Engineer
- R&D Manager
- IP Professional
- Industry Leading Data Capabilities
- Powerful AI technology
- Patent DNA Extraction
Browse by: Latest US Patents, China's latest patents, Technical Efficacy Thesaurus, Application Domain, Technology Topic, Popular Technical Reports.
© 2024 PatSnap. All rights reserved.Legal|Privacy policy|Modern Slavery Act Transparency Statement|Sitemap|About US| Contact US: help@patsnap.com