Fine porous ceramic used as ceramic mold and molding technique
A technology of microporous ceramics and ceramic moulds, which is applied in the direction of ceramic molding machines and manufacturing tools, can solve the problems of high cost, low positioning accuracy, and serious pollution, and achieve the reduction of the number of moulds, high mold precision, and simple production Effect
- Summary
- Abstract
- Description
- Claims
- Application Information
AI Technical Summary
Problems solved by technology
Method used
Image
Examples
Embodiment Construction
[0004] Select hard porcelain and strengthened porcelain raw materials as basic raw materials, slightly reduce or even discard the clay and electrolyte used to adjust the physical properties of raw materials, and add 1%-5% of any organic matter around you (for example: rice, flour, starch, bran, etc.) And the corresponding leavening agent example: flour is added with fermented old noodles at the same time, and rice is added with rice) as raw materials for new molds. After ball milling to achieve the fineness of hard porcelain and reinforced porcelain raw materials, stop ball milling for one to two days, let the yeast further decompose the already very small organic particles, and ball mill again for 6 hours to make the distribution of organic matter more uniform and the raw materials more refined . The raw material is made into a green body according to the requirements of the mold, without glazing or partly glazing as required, and fired according to the requirement that the s...
PUM
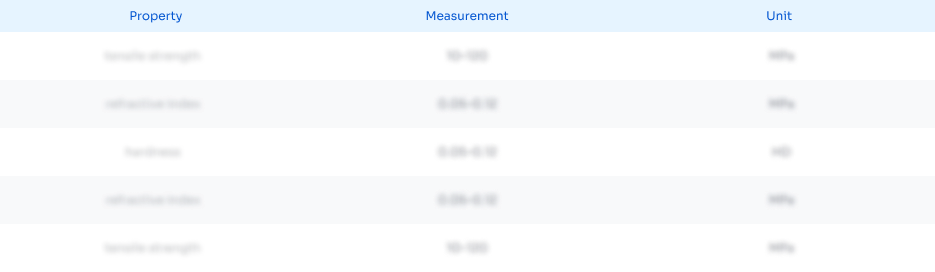
Abstract
Description
Claims
Application Information

- R&D Engineer
- R&D Manager
- IP Professional
- Industry Leading Data Capabilities
- Powerful AI technology
- Patent DNA Extraction
Browse by: Latest US Patents, China's latest patents, Technical Efficacy Thesaurus, Application Domain, Technology Topic, Popular Technical Reports.
© 2024 PatSnap. All rights reserved.Legal|Privacy policy|Modern Slavery Act Transparency Statement|Sitemap|About US| Contact US: help@patsnap.com