Twin-translation-rotation partial decoupling parallel mechanism
A rotating part and two-translation technology, which is applied in manipulators, program-controlled manipulators, manufacturing tools, etc., can solve problems such as complex structure of two-translation-rotation parallel mechanisms, phase coupling between input and output, and complex spatial positions of kinematic pairs. Achieve the effect of easy calibration, small error accumulation and compact structure
- Summary
- Abstract
- Description
- Claims
- Application Information
AI Technical Summary
Problems solved by technology
Method used
Image
Examples
Embodiment 1
[0015] Such as figure 1 The shown two-translation-rotation part decouples the parallel mechanism, the fixed platform 1 is provided with a movable platform 2 , and the movable platform 2 is provided with an end effector 3 . The fixed platform 1 is connected to the moving platform through three different branches, the first branch is provided with an intermediate kinematic pair, and the middle kinematic pair is the rotating pair 5; the kinematic pair directly connected with the fixed platform 1 in the first branch is the rotating pair 4 ; The kinematic pair directly connected with the moving platform 2 in the first branch is a universal hinge 6 . The kinematic pair directly connected with the fixed platform 1 in the second branch is the revolving joint 8 ; the kinematic pair directly connected with the moving platform 2 in the second branch is the ball pair 10 . The third branch is composed of a branch chain with six degrees of freedom in space, and the third branch is provided...
Embodiment 2
[0017] Such as figure 2 The shown two-translation-rotation part decouples the parallel mechanism, and the kinematic pair directly connected with the moving platform 2 in the first branch is the universal hinge 6 . The kinematic pair directly connected with the moving platform 2 in the second branch is a universal hinge 9 . Other structures are the same as those in Embodiment 1, and will not be repeated here.
Embodiment 3
[0019] Such as image 3 The shown two-translation-rotation part decouples the parallel mechanism, and the kinematic pair directly connected with the moving platform 2 in the first branch is the ball pair 7 . The kinematic pair directly connected with the moving platform 2 in the second branch is a universal hinge 9 . Other structures are the same as those in Embodiment 1, and will not be repeated here.
PUM
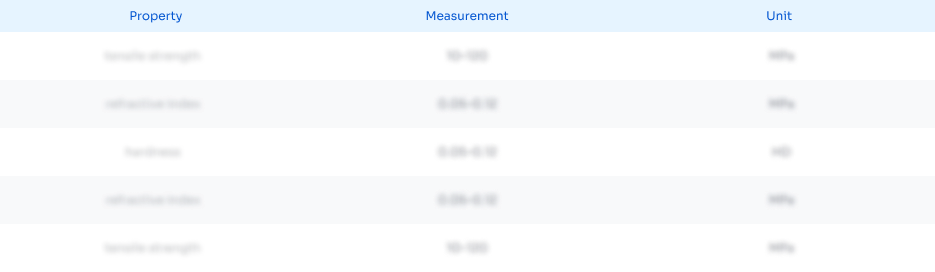
Abstract
Description
Claims
Application Information

- R&D
- Intellectual Property
- Life Sciences
- Materials
- Tech Scout
- Unparalleled Data Quality
- Higher Quality Content
- 60% Fewer Hallucinations
Browse by: Latest US Patents, China's latest patents, Technical Efficacy Thesaurus, Application Domain, Technology Topic, Popular Technical Reports.
© 2025 PatSnap. All rights reserved.Legal|Privacy policy|Modern Slavery Act Transparency Statement|Sitemap|About US| Contact US: help@patsnap.com