Filter element for filtration and manufacturing method thereof
A technology of filter elements and raw materials, which is applied in the field of filter elements for filtration and its production, to achieve the effects of low production cost, safe production process, and reduced industrial costs
- Summary
- Abstract
- Description
- Claims
- Application Information
AI Technical Summary
Problems solved by technology
Method used
Examples
Embodiment 1
[0030] Activated carbon powder (60-325 mesh) 52.5 Silica sol (30% silica content) 21 10% content polyvinyl alcohol
[0031] Aqueous solution 15.7 Ammonium bicarbonate 0.3 Pure water 10.5
[0032] Its preparation method is as follows:
[0033] Weigh each raw material according to the percentage of formula quantity, and the operation steps are as follows:
[0034] ① Mix pure water and activated carbon powder and stir well.
[0035] ②Mix the silica sol and polyvinyl alcohol aqueous solution and stir evenly.
[0036] ③ Add ammonium bicarbonate to the raw materials that have been mixed in step ② and mix well.
[0037] ④ Immediately add the raw materials mixed in step ③ to the raw materials mixed in step ① and mix well.
[0038] ⑤Put the raw materials mixed in step ④ into the pre-prepared mold for stamping or extrusion molding. After standing for 3 hours, put it in the oven and slowly heat up to 160 degrees, and dry the moisture in the mold to shape it. That is, it becomes a po...
Embodiment 2
[0040] Activated carbon powder (60-325 mesh) 35 Zeolite powder (40-325 mesh) 16.3 Silica sol (40% silica content)
[0041] 25.6 10% polyvinyl alcohol aqueous solution 5.1 sodium bicarbonate 2.6 pure water 15.4
[0042] Its preparation method is as follows:
[0043] Weigh each raw material according to the percentage of formula quantity, and the operation steps are as follows:
[0044] ① Mix pure water with activated carbon powder and zeolite powder and stir evenly.
[0045] ②Mix the silica sol and polyvinyl alcohol aqueous solution and stir evenly.
[0046] ③ Add sodium bicarbonate to the raw materials that have been mixed in step ② and mix well.
[0047] ④ Immediately add the raw materials mixed in step ③ to the raw materials mixed in step ① and mix well.
[0048] ⑤Put the raw materials mixed in step ④ into the pre-prepared mold for stamping or extrusion molding. After standing for 3 hours, put it in the oven and slowly heat up to 160 degrees, and dry the moisture in the ...
Embodiment 3
[0050] Activated carbon powder (60-325 mesh) 40 Diatomite (40-325 mesh) 12.3 Silica sol (50% silicon dioxide content) 18.8 2% sodium carboxymethylcellulose aqueous solution 10.5 Sodium bicarbonate 2.7 Pure water 15.7,
[0051] Its preparation method is as follows:
[0052]Weigh each raw material according to the percentage of formula quantity, and the operation steps are as follows:
[0053] ① Mix pure water with activated carbon powder and diatomaceous earth and stir evenly.
[0054] ②Mix the silica sol and sodium carboxymethylcellulose aqueous solution and stir evenly.
[0055] ③ Add sodium bicarbonate to the raw materials that have been mixed in step ② and mix well.
[0056] ④ Immediately add the raw materials mixed in step ③ to the raw materials mixed in step ① and mix well.
[0057] ⑤Put the raw materials mixed in step ④ into the pre-prepared mold for stamping or extrusion molding. After standing for 3 hours, put it in the oven and slowly heat up to 130 degrees, and dr...
PUM
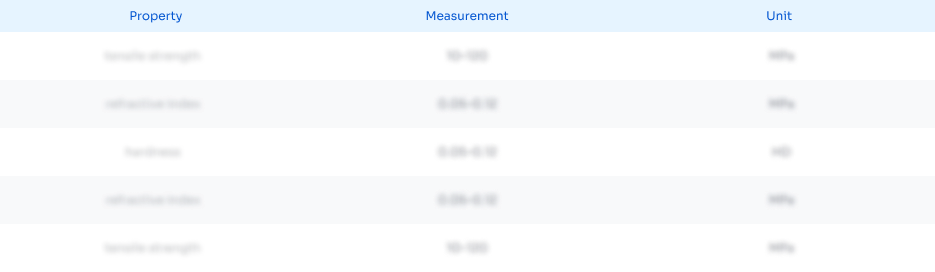
Abstract
Description
Claims
Application Information

- Generate Ideas
- Intellectual Property
- Life Sciences
- Materials
- Tech Scout
- Unparalleled Data Quality
- Higher Quality Content
- 60% Fewer Hallucinations
Browse by: Latest US Patents, China's latest patents, Technical Efficacy Thesaurus, Application Domain, Technology Topic, Popular Technical Reports.
© 2025 PatSnap. All rights reserved.Legal|Privacy policy|Modern Slavery Act Transparency Statement|Sitemap|About US| Contact US: help@patsnap.com