Electric slag liquid pouring method
A casting method and liquid technology, applied in the field of electroslag remelting, can solve the problems of long production cycle, increased production cost, high production cost, etc., and achieve the effects of reducing production cost, improving production efficiency and low production cost
- Summary
- Abstract
- Description
- Claims
- Application Information
AI Technical Summary
Problems solved by technology
Method used
Image
Examples
Embodiment Construction
[0034] The 30-ton converter in the steelmaking plant is used to provide initial molten steel, which is then refined with 30-ton LF.
[0035] The raw materials for slagging mainly include fluorite, industrial alumina and lime, etc. The specific composition requirements are as follows:
[0036] 1) Fluorite: CaF2≥95.0%, SiO2≤2%, S, P≤0.05%, particle size≤5~10mm;
[0037] 2) Alumina: Al2O3≥97%, particle size≤0.5mm;
[0038] 3) Lime: CaO≥90%, SiO2≤2.5%, S, P≤0.05%, particle size 10~20mm;
[0039] 4) Magnesia: MgO≥95%, SiO2≤2.0%, S, P≤0.01%, particle size≤3~5mm;
[0040] 5) Silica: SiO2≥95%, particle size 1~5mm.
[0042] 1) The baking temperature of fluorite, alumina, magnesia, and silica is ≥800°C, and the holding time is ≥8 hours;
[0043] 2) The lime baking temperature is ≥800°C, the holding time is ≥10 hours, and the temperature is not less than 200°C during use.
[0044] figure 2 11-tundish; 12-crystallizer; 13-liquid slag pool; 14-metal mol...
PUM
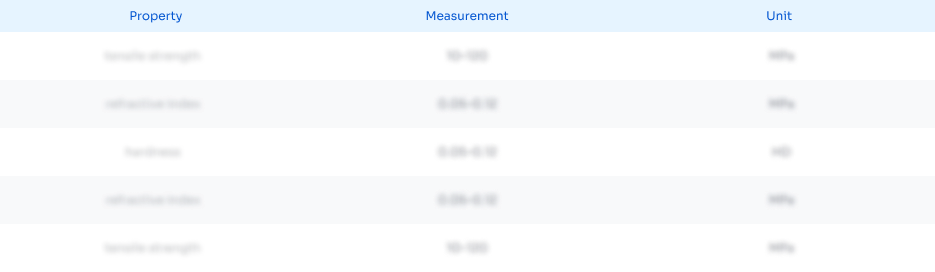
Abstract
Description
Claims
Application Information

- R&D
- Intellectual Property
- Life Sciences
- Materials
- Tech Scout
- Unparalleled Data Quality
- Higher Quality Content
- 60% Fewer Hallucinations
Browse by: Latest US Patents, China's latest patents, Technical Efficacy Thesaurus, Application Domain, Technology Topic, Popular Technical Reports.
© 2025 PatSnap. All rights reserved.Legal|Privacy policy|Modern Slavery Act Transparency Statement|Sitemap|About US| Contact US: help@patsnap.com