Method for district cooling of blast furnace during blast furnace dissection
A zone cooling and blast furnace technology, applied in blast furnaces, blast furnace details, blast furnace parts, etc., can solve problems such as potential safety hazards, imperfect research, and huge cost of manpower and material resources, and achieve the effect of avoiding fragmentation
- Summary
- Abstract
- Description
- Claims
- Application Information
AI Technical Summary
Problems solved by technology
Method used
Image
Examples
Embodiment 1
[0036] A method to cool the blast furnace in sections during dissection, such as Figure 1-2 As shown, the steps are as follows:
[0037] (10) Calibration of zone cooling baseline:
[0038] Predict the temperature distribution of the blast furnace charge based on the data of the temperature probe on the blast furnace, and then predict the boundary line between the solid charge and the melted and softened charge based on the temperature distribution, and mark the blast furnace shell at a position about one meter above the boundary line As the baseline for zoned cooling blast furnaces;
[0039] (11) Drill the cooling medium injection port on the reference line:
[0040] Shut down the furnace, release the high-pressure gas remaining in the blast furnace from the top of the furnace, and detect the residual amount of gas after suitable operation. Drill a hole on the reference line of the zoned cooling blast furnace. The diameter of the hole is 200mm; the depth is to drill through the blas...
Embodiment 2
[0050] Same as Example 1, except that the diameter of the cooling medium injection port is 150mm; the depth is based on drilling through the blast furnace wall; the number is 11; the water speed of the cooling medium injection port is 12m / s, and the pressure of the cooling water is : 1.8MPa.
Embodiment 3
[0052] Same as Example 1, except that the diameter of the cooling medium injection port is 120mm; the depth is subject to drilling through the blast furnace wall; the number is 10; the water speed of the cooling medium injection port is 15m / s, and the pressure of the cooling water is : 2MPa.
[0053] The above-mentioned embodiment of the present invention is used for zone cooling of a 100 cubic meter blast furnace during dissection.
PUM
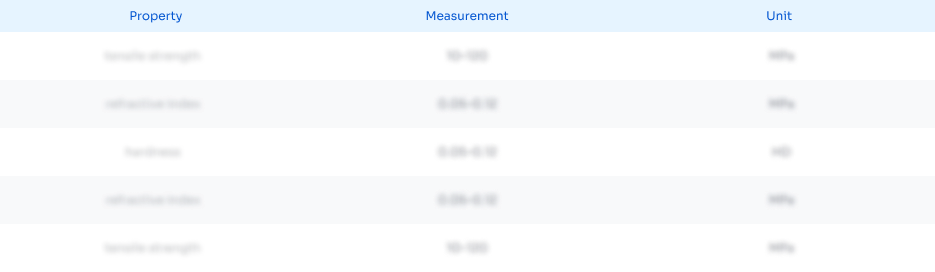
Abstract
Description
Claims
Application Information

- R&D
- Intellectual Property
- Life Sciences
- Materials
- Tech Scout
- Unparalleled Data Quality
- Higher Quality Content
- 60% Fewer Hallucinations
Browse by: Latest US Patents, China's latest patents, Technical Efficacy Thesaurus, Application Domain, Technology Topic, Popular Technical Reports.
© 2025 PatSnap. All rights reserved.Legal|Privacy policy|Modern Slavery Act Transparency Statement|Sitemap|About US| Contact US: help@patsnap.com