Nimble arm of six-DOF robot
A degree of freedom, robot technology, applied in the field of robot arms, can solve the problems of low integration, heavy robot arm, limit the integration of dexterous hands and robot systems, etc., to achieve the effect of high integration, simple structure and light weight
- Summary
- Abstract
- Description
- Claims
- Application Information
AI Technical Summary
Problems solved by technology
Method used
Image
Examples
specific Embodiment approach 1
[0007] Specific implementation mode one: combine Figure 1-Figure 14 Describe this embodiment, the arm of this embodiment is composed of first shoulder joint 1, second shoulder joint 2, first elbow joint 3, second elbow joint 4, two-degree-of-freedom wrist joint 5, base 6, first shoulder joint Connecting part 7, second shoulder joint connecting part 8, upper arm 9, first elbow joint connecting part 10, second elbow joint connecting part 11, forearm 12, first shoulder joint circuit board 14-1, second shoulder joint circuit board 14-2, the first elbow joint circuit board 14-3, the second elbow joint circuit board 14-4, the wrist joint circuit board 14-5 and a plurality of wires 15, and the upper arm 9 and the forearm 12 are provided with inner cavities The first fixed end 1-3 of the first shoulder joint 1 is connected to the base 6, and the first output end 1-4 of the first shoulder joint 1 is connected to the second shoulder joint 2 through the first shoulder joint connector 7....
specific Embodiment approach 2
[0008] Specific implementation mode two: combination Figure 10a-Figure 10c Describe this embodiment, the wiring path between the output end of the first shoulder joint circuit board 14-1 of this embodiment and the input end of the second shoulder joint circuit board 14-2 is: the wire 15 goes around the base 6 from The first axial central hole 1-5 of the first shoulder joint 1 passes through and walks around the shoulder joint connector 7, then passes through the second axial central hole 2-5 of the second shoulder joint 2 and walks around the second Shoulder joint connector 8 penetrates into the inner cavity of upper arm 9, passes through the middle position of the side wall of upper arm 9 and is connected to the input end of the second shoulder joint circuit board 14-2; the output of the first elbow joint circuit board 14-3 The routing path between the terminal and the input end of the second elbow joint circuit board 14-4 is: the wire 15 penetrates from the side wall of the...
specific Embodiment approach 3
[0009] Specific implementation mode three: combination figure 1 , figure 2 , Figure 13 with Figure 14Describe this embodiment, the wiring route between the first output end 1-4 of the first shoulder joint 1 of this embodiment and the first electrical system 1-10 of the first shoulder joint 1 is: the wire 15 runs from the first shoulder The first output end 1-4 of the joint 1 is drawn through the first axial center hole 1-5 of the first shoulder joint 1 to be connected with the first electrical system 1-10 of the first shoulder joint 1; The wiring path between the second output end 2-4 and the second electrical system 2-10 of the second shoulder joint 2 is: the wire 15 is drawn from the second output end 2-4 of the second shoulder joint 2 through the second The second axial central hole 2-5 of the shoulder joint 2 is connected with the second electrical system 2-10 of the second shoulder joint 2; the third output end 3-4 of the first elbow joint 3 is connected with the se...
PUM
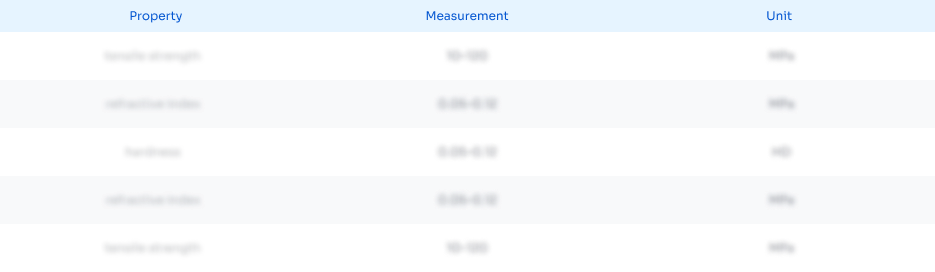
Abstract
Description
Claims
Application Information

- Generate Ideas
- Intellectual Property
- Life Sciences
- Materials
- Tech Scout
- Unparalleled Data Quality
- Higher Quality Content
- 60% Fewer Hallucinations
Browse by: Latest US Patents, China's latest patents, Technical Efficacy Thesaurus, Application Domain, Technology Topic, Popular Technical Reports.
© 2025 PatSnap. All rights reserved.Legal|Privacy policy|Modern Slavery Act Transparency Statement|Sitemap|About US| Contact US: help@patsnap.com