Fiber band reinforced thermoplastic pipe
A thermoplastic, reinforced tube technology, used in rigid tubes, hoses, pipes, etc., to solve problems such as overlapping tape leaks, in-plane and out-of-plane deformation
- Summary
- Abstract
- Description
- Claims
- Application Information
AI Technical Summary
Problems solved by technology
Method used
Image
Examples
Embodiment 1
[0066] Will 3000-denier fibers (purchased from DuPont, USA) were twisted to 80 twists per meter in Z direction, and then three strands of the twisted fibers were plyed and twisted to 50 twists per meter in S direction. The twisted rope is marked as 3000x1x3. Then use the rope to weave a belt on the loom, with a width of 190 mm and a warp direction of 158 3000x1x3 twisted rope, weft is 600 denier polyester fiber with a density of 5 pcs / 10mm. The schematic diagram of the prepared unidirectional tape is shown in Figure 5 shown.
[0067] The obtained unidirectional reinforced tape is passed between two heating plates at a temperature of about 130° C. to shape the polyethylene fibers in the weft direction, and the shaped unidirectional reinforced tape is wound into a coil for use.
[0068] Extrude a high-density polyethylene inner tube at 150°C on an inner tube extruder (purchased from a single-screw plastic tube extruder from Crown Machinery, Germany) (the inner tube diam...
Embodiment 2
[0072] Will 3000-denier fibers (purchased from DuPont, USA) were twisted 80 twists per meter in the Z direction, and the twist coefficient was 1.5. Then three strands of the twisted fibers are plyed again to twist 50 twists per meter in S direction, and the twist coefficient in S direction is 1.65. The twisted rope is marked as 3000x1x3. Then use the rope to weave a belt on the loom, with a width of 95 mm and a warp direction of 79 3000x1x3 twisted rope with 600 denier polyethylene fibers at a density of 5 pcs / 10mm in the weft direction. The schematic diagram of the prepared unidirectional tape is shown in Figure 5 shown.
[0073] The obtained unidirectional reinforced tape is passed between two heating plates at a temperature of about 130° C. to shape the polyethylene fibers in the weft direction, and the shaped unidirectional reinforced tape is wound into a coil for use.
[0074]Extrude a high-density polyethylene inner tube at 150°C on an inner tube extruder (purc...
Embodiment 3
[0078] Will 3000-denier fiber (purchased from DuPont, USA) is twisted in Z direction with 90 twists per meter, and the twist coefficient is 1.5. Then three strands of the twisted fibers are plyed again to twist 30 twists per meter in S direction, and the twist coefficient in S direction is 1.65. The twisted rope is marked as 3000x1x3. Then use the rope to weave a belt on the loom, with a width of 125 mm and a warp direction of 85 3000x1x3 twisted rope, weft of 600 denier polyethylene fibers with a density of 7 threads / 10mm. The schematic diagram of the prepared unidirectional tape is shown in Figure 5 shown.
[0079] The obtained unidirectional reinforced tape is passed between two heating plates at a temperature of about 130° C. to shape the polyethylene fibers in the weft direction, and the shaped unidirectional reinforced tape is wound into a coil for use.
[0080] Extrude a high-density polyethylene inner tube at 150°C on an inner tube extruder (purchased from a ...
PUM
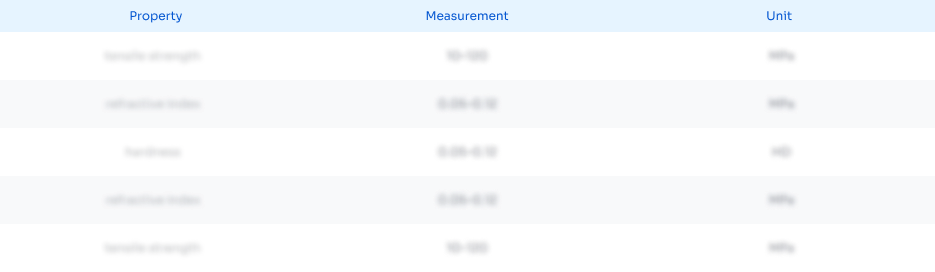
Abstract
Description
Claims
Application Information

- R&D Engineer
- R&D Manager
- IP Professional
- Industry Leading Data Capabilities
- Powerful AI technology
- Patent DNA Extraction
Browse by: Latest US Patents, China's latest patents, Technical Efficacy Thesaurus, Application Domain, Technology Topic, Popular Technical Reports.
© 2024 PatSnap. All rights reserved.Legal|Privacy policy|Modern Slavery Act Transparency Statement|Sitemap|About US| Contact US: help@patsnap.com