Manufacturing method of ball valve body
A manufacturing method and valve body technology, applied in valve details, valve device, valve shell structure and other directions, can solve the problems of affecting the pressure resistance of the valve body, complex manufacturing process, high material cost, saving material cost and low processing cost. , the effect of low production cost
- Summary
- Abstract
- Description
- Claims
- Application Information
AI Technical Summary
Problems solved by technology
Method used
Image
Examples
Embodiment Construction
[0019] Below in conjunction with accompanying drawing and embodiment the present invention will be further described:
[0020] Such as figure 2 As shown, a valve body with a nominal diameter of DN300 is manufactured, and a 500T hydraulic press is used, such as image 3 As shown, the seamless steel pipe of Φ530-550 mm is first cut into a section steel pipe 1 with a length of about 1000 mm, and then the section steel pipe 1 is locally heated, and the heating part is heated from one end to the middle to 800-1000 °C; Then place the heated part of the section material steel pipe 1 downwardly in the lower die 2 for press forging. The die cavity of the lower die 2 is bucket-shaped, and its bucket portion 2a is a bowl-shaped cavity. The bottom of the pipe is penetrated by the straight hole 2b, and through the upsetting of the hydraulic press, the lower end of the segmented steel pipe 1 is formed into a small-diameter constricted circular pipe 3a by press forging, and the constricted...
PUM
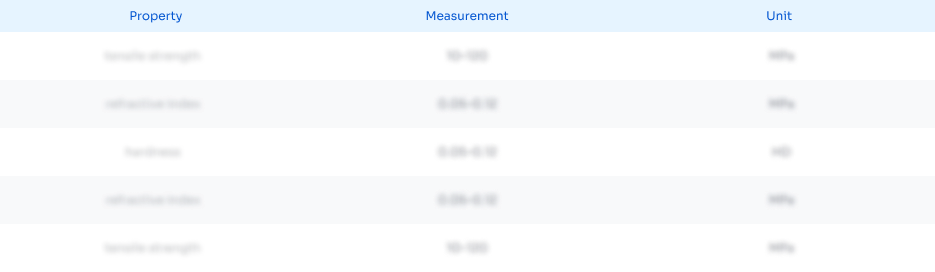
Abstract
Description
Claims
Application Information

- R&D
- Intellectual Property
- Life Sciences
- Materials
- Tech Scout
- Unparalleled Data Quality
- Higher Quality Content
- 60% Fewer Hallucinations
Browse by: Latest US Patents, China's latest patents, Technical Efficacy Thesaurus, Application Domain, Technology Topic, Popular Technical Reports.
© 2025 PatSnap. All rights reserved.Legal|Privacy policy|Modern Slavery Act Transparency Statement|Sitemap|About US| Contact US: help@patsnap.com