Method for separating and extracting 2,3-butanediol
A technology of butanediol and n-butanol, which is applied in the field of butanediol, can solve the problems of liquid-liquid immiscibility area and small operable range, large distribution coefficient, small comparison requirement and theoretical series, and achieve reduction Effects of energy consumption, efficiency improvement, and high recovery rate
- Summary
- Abstract
- Description
- Claims
- Application Information
AI Technical Summary
Problems solved by technology
Method used
Image
Examples
Embodiment 1
[0035] Get 1000g of feed liquid with 12.3% content of 2,3-butanediol, 750g of n-butanol, stir in the mixing tank for 30min, partly lead into the clarifier tank and let it stand for 30min, wait for standing to separate, and send the upper layer extract phase into the refining tank. The distillation tower, while the lower raffinate phase is pumped back to the mixing tank to continue the extraction. The reflux ratio refers to the ratio of the flow rate of the reflux liquid returned to the column from the top of the distillation column to the flow rate of the top product in the rectification operation. The reflux ratio of the rectification tower is selected to be 0.5-1.5, the temperature at the top of the tower is 93°C, and the distillate at the top of the tower is not subjected to phase separation, and all the distillate is pumped back to the mixing tank for further extraction. After a certain period of time, all the feed liquid in the mixing tank was introduced into the clarific...
Embodiment 2
[0037] The overall process is the same as that in Example 1. The 2,3-butanediol content is 9.2% feed liquid 1000g, n-butanol 750g, the selected reflux ratio is 0.5~1.5, after a period of extraction and rectification process, it is recorded that the clarification The mass concentration of 2,3-butanediol in the water phase of the tank was 1.67%, and the extraction cycle operation was stopped. The rectification is continued to separate n-butanol and water, and the content of 2,3-butanediol obtained in the tower reactor is 98.5%, and the extraction rate of 2,3-butanediol in this process can reach 75.32%. The 2,3-butanediol aqueous phase solution containing 1.67% returns to the membrane separation process, and the n-butanol phase is sent to the next extraction and rectification cycle operation, so the loss of 2,3-butanediol will not be caused.
PUM
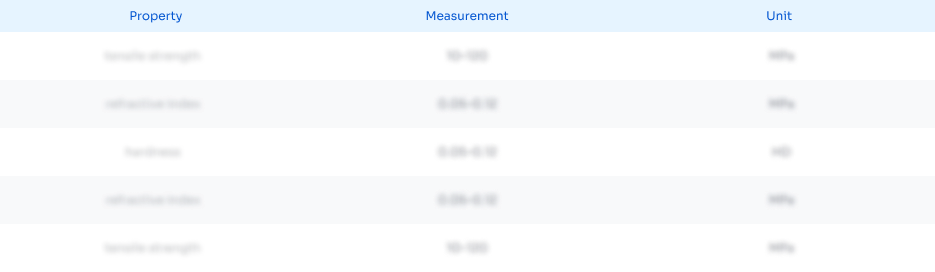
Abstract
Description
Claims
Application Information

- Generate Ideas
- Intellectual Property
- Life Sciences
- Materials
- Tech Scout
- Unparalleled Data Quality
- Higher Quality Content
- 60% Fewer Hallucinations
Browse by: Latest US Patents, China's latest patents, Technical Efficacy Thesaurus, Application Domain, Technology Topic, Popular Technical Reports.
© 2025 PatSnap. All rights reserved.Legal|Privacy policy|Modern Slavery Act Transparency Statement|Sitemap|About US| Contact US: help@patsnap.com