Process for recycling ilmenite through two stages of magnetic separation
A technology for recovering titanium and magnetic separation concentrates, applied in high gradient magnetic separators and other directions, can solve the difficulty of flotation, shorten flotation time, flotation reagent consumption and energy consumption, ilmenite resources cannot be recycled, titanium Low recovery rate and other problems, to achieve the effect of reducing flotation reagent consumption and energy consumption, shortening flotation time, and reducing flotation difficulty
- Summary
- Abstract
- Description
- Claims
- Application Information
AI Technical Summary
Problems solved by technology
Method used
Image
Examples
Embodiment 1
[0063] Embodiment one: use the inventive method to carry out ilmenite beneficiation
[0064] When the selected fine-grained raw material grade is 9.0%, the first-stage high-gradient magnetic separator adopts SSS-1500 type, and when the exciting current is 900A, the obtained concentrate grade is 15.98% and tailings grade is 3.42%; the second-stage high-gradient magnetic separator The concentrator adopts SSS-1500. When the exciting current is 900A, the grade of concentrate ore is 21.30%, and the grade of tailings is 5.44%.
[0065] After the second-stage high-gradient magnetic separation concentrate enters the flotation process, the main agent for flotation (compared with the use of the first-stage high-gradient magnetic separation concentrate as the flotation raw material): the cost of flotation agents can be reduced by 24.7 yuan / ton. The cost of energy consumption can be reduced by 10 yuan / ton · concentrate; the recovery rate of the whole system is increased from 32.28% to 41....
Embodiment 2
[0066] Embodiment two: use the inventive method to carry out ilmenite beneficiation
[0067] In the selection of coarse-grained raw material TiO 2 When the content is 9.0%, the first-stage high-gradient magnetic separator adopts SLON-2000 type. When the excitation current is 900A, the grade of magnetically separated concentrate is 15.81%, and the grade of tailings is 2.82%. The second-stage high-gradient magnetic separator adopts SLON-2000 type, when the excitation current is 900A, the magnetic separation concentrate grade is 21.66%, and the tailings grade is 5.44%.
[0068] After the magnetic separation titanium concentrate enters the flotation process (compared with the use of a high-gradient magnetic separation concentrate as the flotation raw material), the cost of flotation reagents is reduced by 32.65 yuan / ton of concentrate, and the cost of energy consumption is reduced by 8 yuan / tons·concentrate; the recovery rate of the whole system is increased from 34.28% to 44.29...
Embodiment 3
[0069] Embodiment three uses the inventive method to carry out ilmenite beneficiation
[0070] In the selection of full-grain grade raw material TiO 2 When the content is 11%, the first-stage high-gradient magnetic separator adopts SLON-2000 type. When the excitation current is 900A, the grade of magnetically separated concentrate is 17.81%, and the grade of tailings is 3.12%. The second-stage high-gradient magnetic separator adopts SLON-2000 type, when the excitation current is 900A, the magnetic separation concentrate grade is 23.66%, and the tailings grade is 5.92%.
[0071] After the magnetic separation titanium concentrate enters the flotation process (compared with the use of a high-gradient magnetic separation concentrate as the flotation raw material), the flotation flotation agent cost can be reduced by 44.21 yuan / ton concentrate, and the energy consumption cost can be reduced 12 yuan / ton·concentrate; the recovery rate of the whole system increased from 39.38% to 49....
PUM
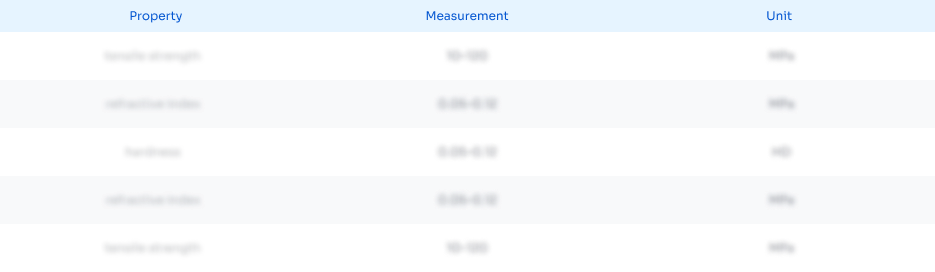
Abstract
Description
Claims
Application Information

- Generate Ideas
- Intellectual Property
- Life Sciences
- Materials
- Tech Scout
- Unparalleled Data Quality
- Higher Quality Content
- 60% Fewer Hallucinations
Browse by: Latest US Patents, China's latest patents, Technical Efficacy Thesaurus, Application Domain, Technology Topic, Popular Technical Reports.
© 2025 PatSnap. All rights reserved.Legal|Privacy policy|Modern Slavery Act Transparency Statement|Sitemap|About US| Contact US: help@patsnap.com