Method for preparing soil-less culture substrate with agriculture and forestry organic waste material and soil-less culture substrate
A technology of soilless cultivation substrate and agricultural and forestry waste, applied in the field of utilization of agricultural and forestry organic waste, can solve the problems of complex material composition, difficult quality control, unstable properties, etc., and achieve stable physical and chemical properties, excellent ventilation performance, pH moderate effect
- Summary
- Abstract
- Description
- Claims
- Application Information
AI Technical Summary
Problems solved by technology
Method used
Image
Examples
Embodiment 1
[0039] 1. Preparation of materials:
[0040] The leaves of the agricultural and forestry wastes were air-dried to a water content of 15%, then pulverized, and then pressed into leaf granules with a diameter of 10-20 mm by using a granulator (Beijing Zhongyi Shenlong Machinery Co., Ltd.).
[0041] 2. Drying treatment:
[0042] Turn on the carbonization machine (Beijing Zhongyi Shenlong Machinery Co., Ltd., SL-II type), heat up to 100 ° C, then add the prepared leaf particles, and dry them at a temperature of 100 ° C to obtain 10% moisture. particles;
[0043] 3. The first pyrolysis treatment:
[0044] Continue heating to increase the temperature in the carbonization machine and maintain it at 150°C, while controlling the oxygen volume percentage in the carbonization machine to be 10%, and carry out the first pyrolysis treatment under the above conditions, wherein the pyrolysis treatment time is for 20min.
[0045] 4. The second pyrolysis treatment:
[0046] Continue heatin...
Embodiment 2
[0066] 1. Preparation of materials:
[0067] The mixed crop straws (wheat straw, sunflower straw and rice straw) were air-dried until the water content was 20%, then pulverized, and then pressed into mixed particles with a diameter of 10 mm by a granulator.
[0068] 2. Drying treatment:
[0069] Turn on the carbonization machine, heat up to 105°C, then add the prepared mixed granules, and dry them at a temperature of 105°C to obtain granules with a moisture content of 8%;
[0070] 3. The first pyrolysis treatment:
[0071] Continue heating to increase the temperature in the carbonization machine and maintain it at 130 ° C, while controlling the oxygen volume percentage in the carbonization machine to be 8%, and perform the first pyrolysis treatment under the conditions, wherein the pyrolysis treatment time 15min.
[0072] 4. The second pyrolysis treatment:
[0073] Continue heating to increase the temperature in the carbonization machine and maintain it at 220 ° C, while c...
Embodiment 3
[0078] 1. Preparation of materials:
[0079] The crop stalks and wheat straws are air-dried until the water content is 15%, then pulverized, and then pressed into mixed granules with a diameter of 15-20 mm by using a granulator.
[0080] 2. Drying treatment:
[0081] Turn on the carbonization machine, heat up to 105°C, then add the prepared mixed granules, and dry them at a temperature of 110°C to obtain granules with a moisture content of 9%;
[0082] 3. The first pyrolysis treatment:
[0083] Continue heating to increase the temperature in the carbonization machine and maintain it at 160°C, while controlling the oxygen volume percentage in the carbonization machine to be 7%, and perform the first pyrolysis treatment under the conditions, wherein the pyrolysis treatment time for 20min.
[0084] 4. The second pyrolysis treatment:
[0085] Continue heating to increase the temperature in the carbonization machine and maintain it at 200 ° C, while controlling the oxygen volum...
PUM
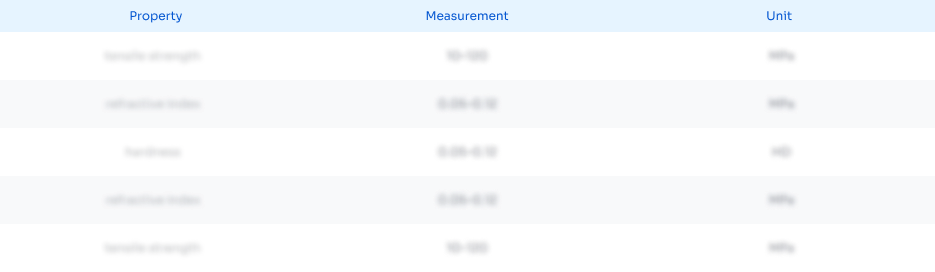
Abstract
Description
Claims
Application Information

- R&D Engineer
- R&D Manager
- IP Professional
- Industry Leading Data Capabilities
- Powerful AI technology
- Patent DNA Extraction
Browse by: Latest US Patents, China's latest patents, Technical Efficacy Thesaurus, Application Domain, Technology Topic, Popular Technical Reports.
© 2024 PatSnap. All rights reserved.Legal|Privacy policy|Modern Slavery Act Transparency Statement|Sitemap|About US| Contact US: help@patsnap.com