Low-temperature aluminum electrolysis process and electrolyte
A technology of electrolyte and aluminum electrolysis, which is applied in the field of electrochemistry and molten salt electrochemical electrolysis, which can solve the problems affecting the stable operation of the electrolytic cell and technical and economic indicators, the increase of the primary crystal temperature of the melt in the cathode area, and the difficulty in forming the furnace side of the electrolytic cell To achieve the effects of reducing energy consumption of aluminum electrolysis, reasonable electrolyte composition, and inhibiting cathode crusting
- Summary
- Abstract
- Description
- Claims
- Application Information
AI Technical Summary
Problems solved by technology
Method used
Examples
Embodiment 1
[0017] Electrolyte melt composition (mass percentage) is 15% K 3 AlF 6 , 61.8% Na 3 AlF 6 , 1.2% Al 2 o 3 , 21% AlF 3 , when 1% LiF is used, the electrolysis temperature used is 910°C, the superheat of the melt is 15°C, the anode effect coefficient is controlled at 0.06 times / cell day, and the anode current density is 0.75A / cm 2 , during the electrolysis process, the initial crystal temperature was tested after sampling the electrolyte at different positions in the electrolytic cell. The problem of cathode crusting caused by the rise of crystal temperature, and the problem of precipitation caused by the drop of alumina dissolution rate can realize the stable operation of the electrolytic cell, the current efficiency can reach 93.2%, and the energy saving and emission reduction are obvious.
Embodiment 2
[0019] Electrolyte melt composition (mass percentage) is 24%K 3 AlF 6 , 45.5% Na 3 AlF 6 , 2.5%Al 2 o 3 , 25% AlF 3 , when 3.0% LiF is used, the electrolysis temperature used is 885°C, the superheat of the melt is 20°C, the anode effect coefficient is controlled at 0.1 times / cell day, and the anode current density is 1.2A / cm 2 , during the electrolysis process, the primary crystal temperature was tested after sampling the electrolyte at different positions in the electrolytic cell. The problem of cathode crusting caused by the rise of crystal temperature, and the problem of precipitation caused by the drop of alumina dissolution rate can realize the stable operation of the electrolytic cell, the current efficiency can reach 92.8%, and the energy saving and emission reduction are obvious.
Embodiment 3
[0021] Electrolyte melt composition (mass percentage) is 20.0% K 3 AlF 6 , 51.0% Na 3 AlF 6 , 2.0% Al 2 o 3 , 23.0% AlF 3 , 4.0% LiF, the electrolysis temperature used is 850°C, the superheat of the melt is 40°C, the anode effect coefficient is controlled at 0.01 times / cell day, and the anode current density is 0.5A / cm 2 , during the electrolysis process, the initial crystal temperature was tested after sampling the electrolyte at different positions in the electrolytic cell. The problem of cathode crusting caused by the rise of crystal temperature and precipitation caused by the drop of alumina dissolution rate can realize the stable operation of the electrolytic cell, the current efficiency can reach 94.5%, and the energy saving and emission reduction are obvious.
PUM
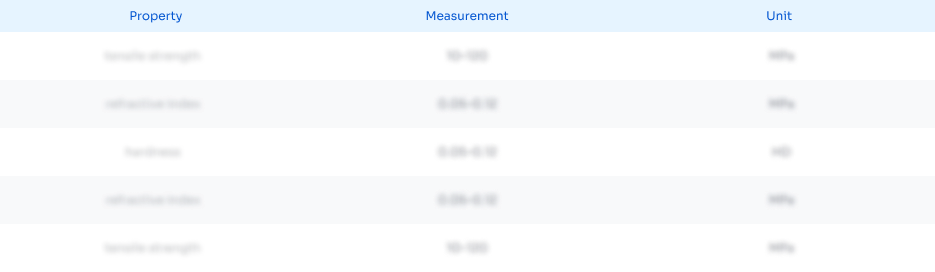
Abstract
Description
Claims
Application Information

- R&D
- Intellectual Property
- Life Sciences
- Materials
- Tech Scout
- Unparalleled Data Quality
- Higher Quality Content
- 60% Fewer Hallucinations
Browse by: Latest US Patents, China's latest patents, Technical Efficacy Thesaurus, Application Domain, Technology Topic, Popular Technical Reports.
© 2025 PatSnap. All rights reserved.Legal|Privacy policy|Modern Slavery Act Transparency Statement|Sitemap|About US| Contact US: help@patsnap.com