Method for designing rotary feed-in mechanism of double-roller cold pilger mill and device thereof
A technology of cold rolling mill and feeding mechanism, which is applied in the direction of metal rolling, metal rolling, metal processing equipment, etc. It can solve the problems of large impact load, high noise, and difficult processing and assembly of the transmission mechanism, so as to overcome the impact The effect of large load, convenient maintenance and compact layout
- Summary
- Abstract
- Description
- Claims
- Application Information
AI Technical Summary
Problems solved by technology
Method used
Image
Examples
Embodiment 1
[0016] Such as figure 1 As shown, three worm gear-worm transmissions, a first worm shaft 5, a second worm shaft 9 and a third worm shaft 13 are provided on the revolving feed box 16. The first servo motor 1 communicates with the first worm shaft through the coupling 3 The shaft 5 is connected, the worm wheel 6 meshes with the first worm shaft 5, the worm wheel 6 is installed on the left and right first shafts 7 through a key connection, and the left and right first shafts 7 are connected with the left and right lead screws 10 through a coupling to realize the first servo motor 1 The left and right lead screws 10 are driven to move forward. The second servo motor 2 is connected to the second worm shaft 9 through a coupling, the worm gear meshes with the second worm shaft 9, the worm gear is connected to the second shaft 8 through a key connection, and the second shaft 8 is connected to the optical rod 11 through the coupling It is connected with the tube blank chuck 12 to realiz...
Embodiment 2
[0018] The servo motor drives the screw 10 to feed in another way, such as figure 2 Shown. Three worm gear-worm transmissions, a first worm shaft 5, a second worm shaft 9 and a third worm shaft 13 are provided on the rotary feed box 16, and the first servo motor 1 is connected to the first worm shaft 5 through a coupling 3 , The worm wheel 6 meshes with the first worm shaft 5, the worm wheel 6 is installed on the right first shaft 7 through a key connection, and the right first shaft 7 is connected with the right screw 10 through a coupling, so that the first servo motor 1 drives the right screw The bar 10 is sent into motion. The third servo motor 14 is simultaneously connected to the third worm shaft 13 through the coupling 3, the worm wheel 6 meshes with the third worm shaft 13, the worm wheel 6 is mounted on the first shaft 7 on the left by a key connection, and the first shaft 7 on the left is connected by the coupling The shaft device is connected with the right screw 1...
Embodiment 3
[0021] The third method used by the servo motor to drive the lead screw 10 to feed movement, such as image 3 Shown, with figure 2 The difference is that the rotary feeding box 16 is driven by four servo motors, the first servo motor 1, the second servo motor 2 and the third servo motor 14 are driven by three servo motors to drive the lead screw 10 to feed and the light rod 11 to rotate. The fourth servo motor 15 directly drives the gear transmission connected to the mandrel clamping mechanism 4, instead of being powered by the rotary feeding mechanism.
PUM
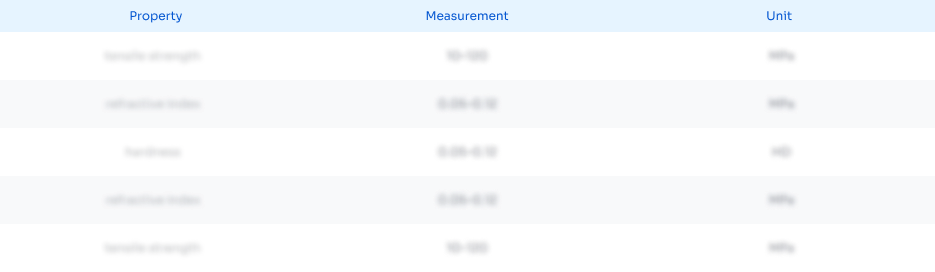
Abstract
Description
Claims
Application Information

- R&D
- Intellectual Property
- Life Sciences
- Materials
- Tech Scout
- Unparalleled Data Quality
- Higher Quality Content
- 60% Fewer Hallucinations
Browse by: Latest US Patents, China's latest patents, Technical Efficacy Thesaurus, Application Domain, Technology Topic, Popular Technical Reports.
© 2025 PatSnap. All rights reserved.Legal|Privacy policy|Modern Slavery Act Transparency Statement|Sitemap|About US| Contact US: help@patsnap.com