Large flow jet servo valve driven by giant magnetostrictive actuator
A giant magnetostrictive and actuator technology, applied in servo motor components, fluid pressure actuation devices, mechanical equipment, etc., can solve the problems of low natural frequency of torque motor, limited response speed capability, large inertia of jet tube, etc. The effect of strong driving ability, large output force and high control precision
- Summary
- Abstract
- Description
- Claims
- Application Information
AI Technical Summary
Problems solved by technology
Method used
Image
Examples
Embodiment Construction
[0024] Such as figure 1, as shown in 2 and 3, the new jet servo valve includes a magnetic rod 8, a left end cover 7, a right end cover 15, a thermal compensation cover 4, and a thermal compensation slider 6, which are installed in the thermal compensation cover 4 and the thermal compensation slider 6 The giant magnetostrictive rod 3, the output slider 2, the preload spring 13, the coil bobbin 5 located outside the thermal compensation cover 4 and the thermal compensation slider 6, and the driving coil 23 and the bias coil wound around the coil bobbin 5 in turn Set the coil 11;
[0025] The new jet servo valve designs a new type of giant magnetostrictive actuator between the nozzle and the receiver of the traditional deflector type jet tube servo valve, and the actuator drives the output slider 2 to replace the original deflected jet tube servo valve torque motor and its Driven deflector, the new servo valve output slider 2 is directly driven by the giant magnetostrictive actu...
PUM
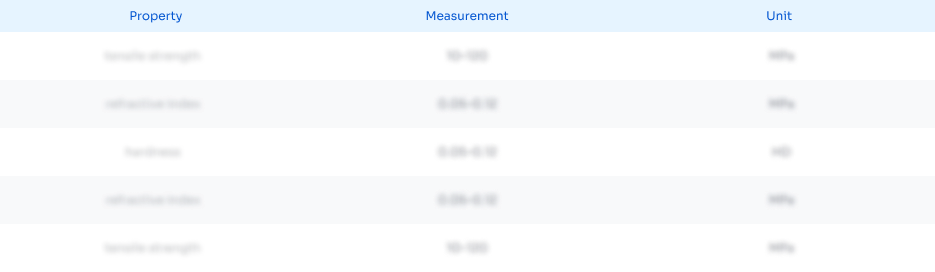
Abstract
Description
Claims
Application Information

- R&D Engineer
- R&D Manager
- IP Professional
- Industry Leading Data Capabilities
- Powerful AI technology
- Patent DNA Extraction
Browse by: Latest US Patents, China's latest patents, Technical Efficacy Thesaurus, Application Domain, Technology Topic, Popular Technical Reports.
© 2024 PatSnap. All rights reserved.Legal|Privacy policy|Modern Slavery Act Transparency Statement|Sitemap|About US| Contact US: help@patsnap.com