Method for producing stepped PCB board
A technology of a PCB board and a production method, which is applied in the production field of stepped PCB boards, can solve the problems of difficulty in precise positioning of stepped grooves, difficulty in accurately controlling the size and depth of stepped grooves, and difficulty in ensuring that the walls of the stepped grooves are neat and free of defects, etc. The effect of positioning, controllable cutting depth and less process
- Summary
- Abstract
- Description
- Claims
- Application Information
AI Technical Summary
Problems solved by technology
Method used
Image
Examples
Embodiment 1
[0026] The production method of ladder PCB board comprises the following steps:
[0027] Such as Figure 4 As shown, a, the inner layer core plate 4 has a window 41;
[0028] b. The first prepreg 3 and the second prepreg 5 are pasted on both surfaces of the inner core board 4 respectively, the first prepreg 3 pre-opens the window 31, the second prepreg 5 pre-opens the window 51, the positions of the window 31, the window 51 and the window 41 Alignment; after this step is completed, the inner core board 4 is sandwiched between the first prepreg 3 and the second prepreg 5;
[0029] c. Put the silica gel sheet 7 into the windows 31, 41, and 51; the thickness of the silica gel sheet 7 is approximately equal to the sum of the thicknesses of the first prepreg 3, the inner core board 4 and the second prepreg 5.
[0030] d, the first outer layer core board 2 is arranged on the surface of the first prepreg 3, and the second outer layer core board 6 is arranged on the surface of the s...
Embodiment 2
[0036] Such as Figure 6 Shown is the side cross-sectional view before cutting after the components of the PCB board in Example 2 are superimposed. On the basis of Example 1, a third prepreg 8 is attached to the surface of the first outer core board 2, a first copper foil 9 is attached to the surface of the third prepreg 8, and a fourth prepreg is attached to the surface of the second outer core board 6. 10. A second copper foil 11 is attached on the surface of the fourth prepreg 10 . All the other steps are the same as in Example 1.
Embodiment 3
[0038] On the basis of Example 2, both the first copper foil and the second copper foil are replaced by core boards. Other steps and structure are identical with embodiment 2.
PUM
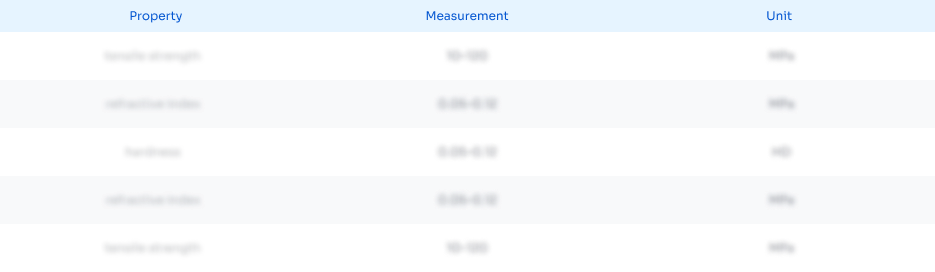
Abstract
Description
Claims
Application Information

- R&D
- Intellectual Property
- Life Sciences
- Materials
- Tech Scout
- Unparalleled Data Quality
- Higher Quality Content
- 60% Fewer Hallucinations
Browse by: Latest US Patents, China's latest patents, Technical Efficacy Thesaurus, Application Domain, Technology Topic, Popular Technical Reports.
© 2025 PatSnap. All rights reserved.Legal|Privacy policy|Modern Slavery Act Transparency Statement|Sitemap|About US| Contact US: help@patsnap.com