Large-working space parallel robot mechanism
A working space and robot technology, applied in manipulators, manufacturing tools, program-controlled manipulators, etc., can solve the problems of small working space of the moving platform, inability to realize rotation of the moving platform, and limit the application of parallel robots, so as to reduce the space required for installation, The effect of simplifying the design
- Summary
- Abstract
- Description
- Claims
- Application Information
AI Technical Summary
Problems solved by technology
Method used
Image
Examples
Embodiment Construction
[0027] The present invention will be further described below in conjunction with the accompanying drawings and specific embodiments.
[0028] Such as Figure 3 to Figure 7 As shown, a large working space parallel robot mechanism 300 includes a base 31 , a branch chain 32 , a moving platform 33 and a driving device 34 . The base 31 is the installation basis of the associated robot mechanism 300 of the present invention, which supports the weight of each branch chain 32 , moving platform 33 and end effector. The drive device 34 includes a linear drive device and a rotary drive device, which are set according to the actual movement requirements of the branch chain 32 . The driving device 34 is connected with the branch chain 32 to control the active state of the branch chain 32 , that is, the linear movement state or the rotation state, so as to further change the geometric position of the moving platform 33 according to the geometric connection relationship of the branch chain ...
PUM
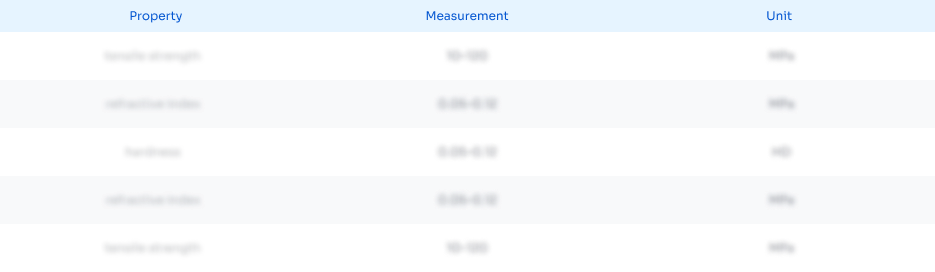
Abstract
Description
Claims
Application Information

- R&D
- Intellectual Property
- Life Sciences
- Materials
- Tech Scout
- Unparalleled Data Quality
- Higher Quality Content
- 60% Fewer Hallucinations
Browse by: Latest US Patents, China's latest patents, Technical Efficacy Thesaurus, Application Domain, Technology Topic, Popular Technical Reports.
© 2025 PatSnap. All rights reserved.Legal|Privacy policy|Modern Slavery Act Transparency Statement|Sitemap|About US| Contact US: help@patsnap.com