Method for quantitative stock level-lowering and blowing out of blast furnace
A technology for lowering material surface and blast furnace, which is applied to blast furnaces, blast furnace details, furnaces, etc. It can solve the problems of frequent knocking, waste of resources, threats to the safety, high efficiency, and environmental protection of the process of stopping the furnace at the material lowering surface, so as to eliminate threats and reduce wasteful effect
- Summary
- Abstract
- Description
- Claims
- Application Information
AI Technical Summary
Problems solved by technology
Method used
Image
Examples
Embodiment Construction
[0032] On July 31, 2009, the No. 3 blast furnace lowered its material surface to the tuyere zone, and shut down the furnace for a 3-day planned maintenance, spraying lining from the lower edge of the furnace throat steel tile to the belly of the furnace. Before shutting down, based on the quantitative principle of shutdown technology at the falling material level, combined with the specific conditions of the blast furnace shutdown, the nodes and control principles of each stage in the process of shutting down the material level were calculated and planned, and the level of material falling was refined. Parameters of the shutdown process.
[0033] Table 1 Quantitative control parameters of blast furnace shutdown at the falling surface
[0034]
[0035] Table 2 Quantitative operating parameters of blast furnace shutdown at the material lowering surface
[0036]
[0037]From 8:00 to 10:00 on July 30, the blast furnace was shut down for minor repairs, and at 10:00 the air w...
PUM
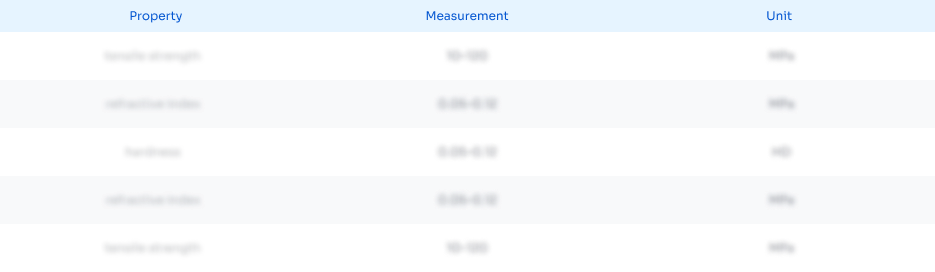
Abstract
Description
Claims
Application Information

- Generate Ideas
- Intellectual Property
- Life Sciences
- Materials
- Tech Scout
- Unparalleled Data Quality
- Higher Quality Content
- 60% Fewer Hallucinations
Browse by: Latest US Patents, China's latest patents, Technical Efficacy Thesaurus, Application Domain, Technology Topic, Popular Technical Reports.
© 2025 PatSnap. All rights reserved.Legal|Privacy policy|Modern Slavery Act Transparency Statement|Sitemap|About US| Contact US: help@patsnap.com