Self-adapting morphing trailing edge based on SMA
A variant wing, self-adaptive technology, applied in the direction of heat reduction structure, etc., can solve the problems of inability to realize automatic control, no drive unit, deflection angle limitation, etc., to achieve the effect of reducing weight, increasing driving force, and improving deformation efficiency
- Summary
- Abstract
- Description
- Claims
- Application Information
AI Technical Summary
Problems solved by technology
Method used
Image
Examples
Embodiment Construction
[0018] The SMA-based adaptive variant wing trailing edge structure of the aircraft of the present invention is based on a certain unmanned aerial vehicle wing trailing edge airfoil, and a structural model designed based on experimental data of the airfoil, including epoxy The wing trailing edge structure composed of resin plate wing ribs, aluminum alloy long trusses, rigid beams and a drive system composed of shape memory alloy (SMA). The structure-driven scheme of the present invention is as figure 1 As shown, the deflection of the trailing edge structure of the wing is achieved through the cumulative effect of multiple articulated chains. Among them, unit one and unit two form joint one; unit two and unit three form joint two; unit three and unit four form joint three. The drive system is composed of parallel SMA wires, which are fixed on the stringer between the two wing ribs (embedded with epoxy resin for insulation treatment). Considering the flight conditions that simulat...
PUM
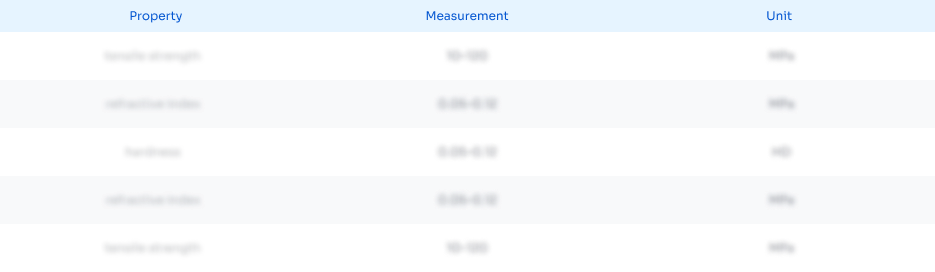
Abstract
Description
Claims
Application Information

- R&D
- Intellectual Property
- Life Sciences
- Materials
- Tech Scout
- Unparalleled Data Quality
- Higher Quality Content
- 60% Fewer Hallucinations
Browse by: Latest US Patents, China's latest patents, Technical Efficacy Thesaurus, Application Domain, Technology Topic, Popular Technical Reports.
© 2025 PatSnap. All rights reserved.Legal|Privacy policy|Modern Slavery Act Transparency Statement|Sitemap|About US| Contact US: help@patsnap.com